Delaminations in plastic package:Evolution under constraints
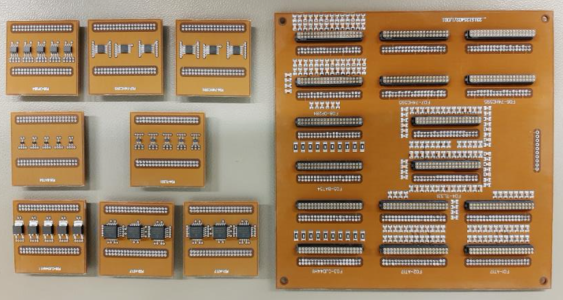
The various players in the space sector activities (equipment manufacturers, operators, and space agencies) believe that the future belongs to industrial components. Industrial components (such as Automotive-quality and commercial-quality components) have already been selected and used for launcher-type or short duration satellite missions. Metallographic cross sections made on plastic packages industrial components, in the frame of these programs, revealed delamination between the chip and the encapsulation resin. Delamination has generally been accepted for short-term missions because it ‘'has not enough time’' to worsen after application of mechanical vibration due to the launch phase and due to the short duration of the mission ; but this acceptation is questioned for long-term applications such as conventional satellites We also know that these defects-delamination- are more likely to evolve during long term thermal cycling, where the length of delamination of all types will increase, sometimes reaching out to the external sides of the packages, allowing potential corrosion of the bonding and dice. Long term space missions expose equipment to thermal stresses, especially repeated thermal cycles, which are present in all kind of satellites missions. These permanent thermal cycling combined with the operating phases of the equipment (ON-OFF), causes thermomechanical stresses in the components and affect the component (and equipment) reliability. Today, we do not have enough experience to estimate what is the level of degradation of industrial plastic packaged parts (COTS) at the end of long term space mission.