High efficiency 150 K Joule-Thomson cryocooler with an ejector
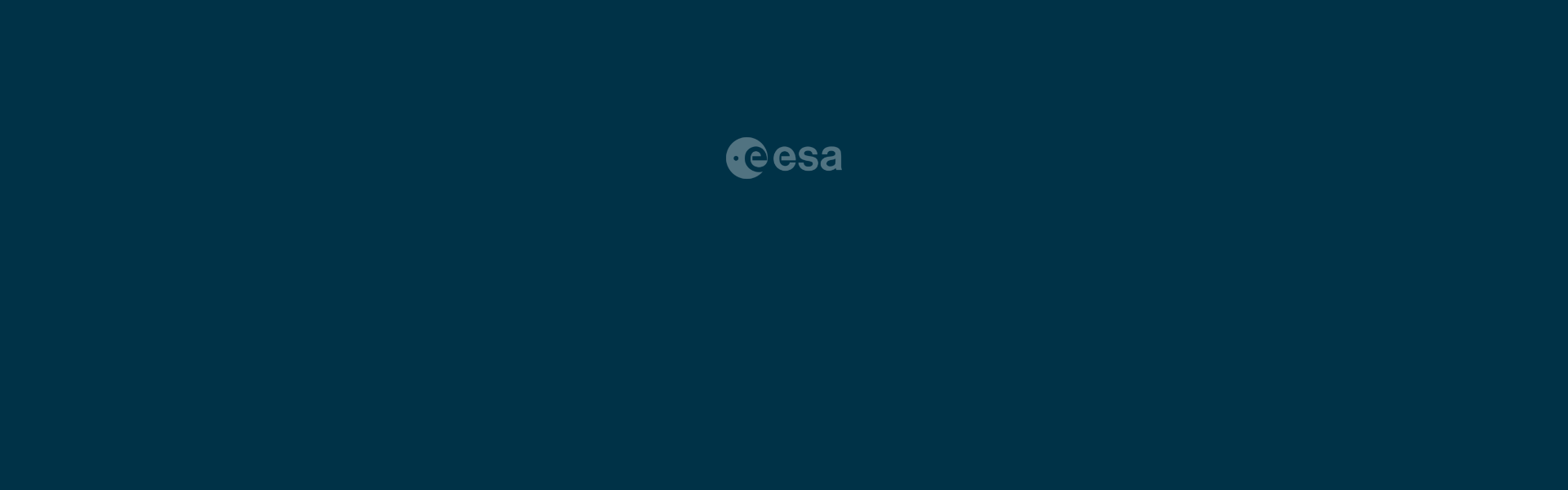
There is an increasing need for ever smaller pulse-tube coolers. These coolers have the characteristics necessary for space applications because the absence of moving parts in the cold finger makes them extremely reliable and any induced vibrations are typically smaller and easier to control.
But these types of cooler are less efficient and have a lower power density. Typically, this is resolved by increasing their drive frequency, to reduce amplitudes and displacements, which means that the coolers are smaller
Unfortunately, at higher frequencies the thermal and flow losses increase as well. A new de-risk framework activity has investigated these losses, together with ways to improve optimisation
Three potential cold finger configurations were designed and met performance requirements. The designs chosen will be beneficial for a wide range of coolers, from high-end ‘full space’ coolers to series produced ‘COTS+’ coolers for low-cost missions.
The activity investigated design options for miniaturisation of pulse-tube cold fingers, and simulated and optimised for efficiency before experimentally verifying the predicted performance through breadboard testing.
There is an increasing need for ever smaller pulse-tube coolers. These coolers have the characteristics necessary for space applications because the absence of moving parts in the cold finger makes them extremely reliable and any induced vibrations are typically smaller and easier to control.
But these types of cooler are less efficient and have a lower power density. Typically, this is resolved by increasing their drive frequency, to reduce amplitudes and displacements, which means that the coolers are smaller
Unfortunately, at higher frequencies the thermal and flow losses increase as well. A new de-risk framework activity has investigated these losses, together with ways to improve optimisation
Three potential cold finger configurations were designed and met performance requirements. The designs chosen will be beneficial for a wide range of coolers, from high-end ‘full space’ coolers to series produced ‘COTS+’ coolers for low-cost missions.
The activity investigated design options for miniaturisation of pulse-tube cold fingers, and simulated and optimised for efficiency before experimentally verifying the predicted performance through breadboard testing.