Improvement of sample containment/handling for volatile analysis
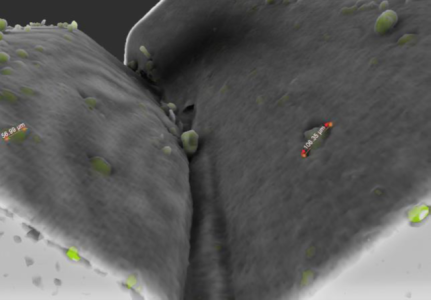
The objective is to design, build and develop a oven sealing mechanism breadboard incl. oven, which shall provide reliable sealing of high temperature ovens up to 1000C, in a moon analogue dusty environment, with leak rates of 10-5sccm/ls or better. This will improve robustness and performance of currently available oven technology used for Pyrolysis, DSC and geochronology experiments.
Heating samples to extract volatiles is a standard way to characterise solid samples. By heating a sample and recording the temperature profile results it can explain a lot about the nature of those volatiles and allow them to be collected and analysed further. This technique is, in principle, a standard process in terrestrial laboratories and the same principle is applied in-situ for planetary analysis where solid samples are delivered to an oven, which is sealed and heated to produce signatures of the volatiles. Several planetary mission instruments, such as those on Viking, Beagle II, Rosetta and Curiosity all use this technique but have shown that developing an oven with a strong sealing mechanism, which is both lightweight and robust, is challenging. This is especially true in environment such as the lunar surface, where the pervasive nature of the dust has the potential to interfere with the tight seal. Large, expensive hardware such as that on the Curiosity rover can have extensive dust mitigation in place to prevent this, but this is not a feasible solution for smaller more mass restricted hardware such as that on Rosetta.
An activity with TDE and the Open University, UK has developed, tested and validated a reliable and re-usable sealing and heating mechanism, which ensured sufficiently low leak rates and heating performance up to 1000oC of the sample in a dusty environment. The oven can provide reliable and reusable heating and sealing using pyrolysis, as the activity identified a mechanism that could seal under a relatively low compressive force (~400N) and maintain integrity, even in the presence of dust, while at the same time allowing a sample to be heated to 1000°C.
The activity, through a combination of existing oven designs and investigation into the performance of different seal gasket materials and geometry, was able to determine that seals compressed between two symmetrical 90° knife edges were able to close even in the presence of up to 9 per cent dust coverage. The testing also demonstrated that using polytetrafluoroethylene (PTFE) less than 2 mm thick, was capable of resealing at least five times before it failed.
This technology, if further developed, can be used in all future missions where sealing force or dust mitigation measures (or both) are limited.
Current experience from ExoMars shows the shortcomings for a Tapping Station (TS) based design for volatile sample analysis/pyrolysis. It is perceived that the oven/sampling system used in a dusty environment needs to be more robust. Dust environment PLUS high temperature volatile analysis ( isotopic analysis of mineral matrices, like K-Ar dating for geochronology...) poses a challenge on the oven/sealing mechanism. A separation of the sealing and the high temperature part of a pyrolysis oven seems most appropriate but runs the risk of increased mass/volume compared to the current TS approach. The objective of this activity is to design, build and test a representative breadboard which increases the robustness of such a sampling system for temperatures up to 1000C. extensive tests shall be performed in the course of this activity.