Assessing the use of AM: AM of a Flywheel for High Performance Reaction Wheel
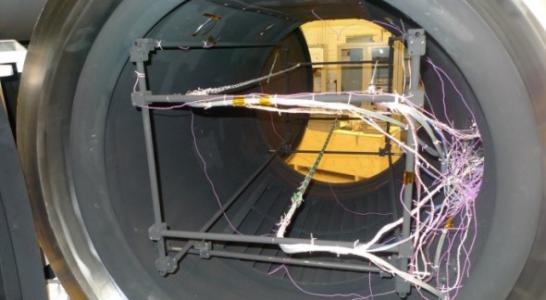
Due to an increasing power and complexity, electrical harnesses in aerospace systems require mass and volume optimization. The harness mass performance is driven by the ampacity (or current rating), that is the maximum current a wire or cable is able to carry without exceeding its maximum operating temperature. This current depends on the environment (pressure, temperature…), the wire’s physical characteristics (gauge, dielectric, overall diameter…) but also on the number of wires routing in the same bundle.
The new rules improve the precision of the wire’s thermal model. In addition, they allow taking into account the environment temperature and the exact physical characteristics of the wires.
In most cases a mass and volume reduction of harness bundles is to be expected. Mass savings in the range 20% to 50% could be expected on power bundles depending of the use cases. The savings on current sizing exceed 90% for some of the wires.
The assumptions for application of the new derating rules are more clearly defined and justified.
In addition to the new single wires and bundle derating rules, it is now proposed to allow thermal simulations for harness sizing based on worst case wire temperatures, provided that the simulation software complies with specified criteria. This approach permits specific harness configurations and additional significant optimizations.