New packaging techniques to increase power density of power control and distribution units
Programme
GSTP
Programme Reference
GT17-343EP
Prime Contractor
ASP GMBH
Start Date
End Date
Status
Closed
Country
Germany
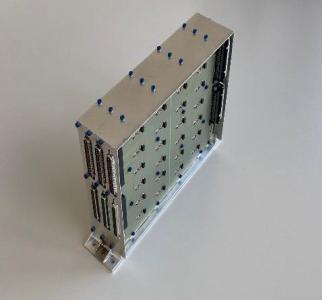
Objectives
The aim of the activity is to explore new materials and packaging/integration possibilities for power units to in order to maximize heat transfer and minimize volume.
Description
Power units have been using the same integration system since decades. It is based on a vertical module approach that limits considerably the thermal access to the baseplate. Moreover, some of the modules have very low dissipation but still use the same system. As a consequence, these modules occupy some precious space that is scarce for the high power consumers. This becomes a limiting factor in high dissipation units. Power units like Power Conditioning Units (PCDU) and Power Propulsion Units for Electrical Propulsion (PPU) easily dissipate more 300W. At system level (Satellite) a dedicated radiator of 1m^2 is needed to cool down a unit of 300W with an interface temperature of 50 degC.
The activity will try to find new mechanical concepts that maximize the space allocated to the high dissipative modules by placing the low dissipative ones farther away. To achieve this, new materials and new thermal concepts will be needed. Internal micro-heat pipes or improved thermal paths need to be explored. The main goal is to improve the unit?s power density, making them smaller and lighter. There can be some impacts at system level that need to be studied since, once evacuated from the unit, the heat has to be harnessed to the radiators. If the heat density is higher, there could be limitations on that side. Hence, the heat spread should be better than the current one in order to reduce that density and limit, or even improve the impact at system level. For instance, by eliminating the cold plate or the external heat pipes.
The objective could be achieved if the modularity approach changes from vertical to horizontal (or combined vertical/horizontal) so that there is ample room for power dissipative components to be mounted close to the radiators. Due to this new concept, also components not mounted directly on baseplate can benefit from the "shorter"(=improved) thermal path. Taking inspiration from automotive industry, new packaging techniques have to be studied and tried out on space units. Also new internal (modules) connection concept has to be develop, maybe in the form of ?grid? or ?matrix?.
The optimized thermal interface between power unit and satellite radiator is expected to lead to mass savings around 30 %, with target unit volume reduction of 25%. The achievable power density could be more than double of the actual one.
The main tasks that will be done in this activity are:
- Define Thermal Mechanical constraints at system level for several study cases
- Study of possible alternative Thermal Mechanical solutions
- Selection of a study case and of the most promising thermo?mechanical concept and define Engineering Model (EM) requirements.
- Detailed Design and Analysis of the Thermo-Mechanical Engineering Model
- Validation of the manufacturing and Assembly, Integration and Test processes using the EM
- EM Thermo-Mechanical Test
Application Domain
GEN-Generic Technologies
Technology Domain
21-Thermal
3-Space Systems Electrical Power
Competence Domain
4-Electric Architecture, Power and Energy, EMC
Initial TRL
TRL 2
Target TRL
TRL 6
Achieved TRL
TRL 5
Public Document
Executive Summary
Final Presentation