Applied NDI methods for quality assurance of high density AM mission critical parts
Programme
GSTP
Programme Reference
GT14-402MS
Prime Contractor
FORCE TECHNOLOGY
Start Date
End Date
Status
Contracted
Country
Denmark
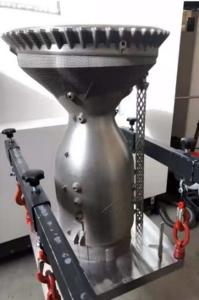
Objectives
The objectives of this activity are to develop and demonstrate high energy x-ray (betatron) imaging as a feasible method for quality control of mission critical dense AM components that have a tubular open structure to allow half-length inspection via a small linear array detector.
Description
Additive manufacturing (AM) is developing at an impressive pace, especially for mission critical components like combustion chambers and turbopumps. However, new inspection methods during manufacturing become a necessity as failure of such components leads to a failure of the entire launch vehicle.
;
The activity aims to push the limit towards higher detection levels for such ?open structures? by including a-priori knowledge of the CAD reconstruction model and using a scanner configuration, where a small-sized linear array detector is maneuvered inside the AM structure. Thus, only transmitting through ?half the thickness?. As example, a donut-shaped structure can then be inspected by placing the detector in the center hole and the x-ray source on the outside and then rotate it by a full revolution. Instead of a traditional one, a Betatron high-energy x-ray source is chosen. It is more compact, flexible and cost-effective and can better penetrate thick sections. The safety aspect will be a significant part of the activity as shielding from the radiation is a critical issue.
;
In a previous ESA activity intended for quality control of AM parts in the launcher fabrication a proof-of-concept reached TRL3, demonstrating NDI of single section of a Inconel AM turbine manifold of the ESA Prometheus engine. It also demonstrated the use of Betatron and validated the CIVA software that allows stochastic simulations of billions of x-ray photons to most accurately simulate the performance of any variations of the x-ray systems. The benefits of using the principle of a small detector inside the inspected object, for inspection of large dense structures described above were demonstrated in late 2019.
;
The goal is to reach TRL 5 by performing a full inspection of a high density AM trust chamber with a 2D radiography and 3D tomography, acting as a demonstration of the NDI method. It is achieved by completing following tasks:
-
- Technical survey of state-of-art 3D tomography to update current knowledge on NDI methods on AM parts.
- Requirement specification
- Simulation with CIVA including detailed description of beam characteristics, CAD design, material properties etc. in order to optimize the conditions for a physical inspection.
- Developing an inspection strategy and logic based on 2D digital X-ray and 3D semi-Computer-Tomography.
- Design, manufacturing and testing of compact line array detector and integrating it together with the Betatron x-ray source in the inspection cell
- Demonstration on complete thrust chamber
Following this activity, it is intended to automate the inspection cell and upgrade the inspection facility, maturing the process into a fully commercial service.
Application Domain
Space Transportation
Technology Domain
24 - Materials and Manufacturing Processes
Competence Domain
2-Structures, Mechanisms, Materials, Thermal
Initial TRL
TRL 3
Target TRL
TRL 5
Achieved TRL
TRL N/A