Compatibility of Welded Propellant Systems with New Green Propellants
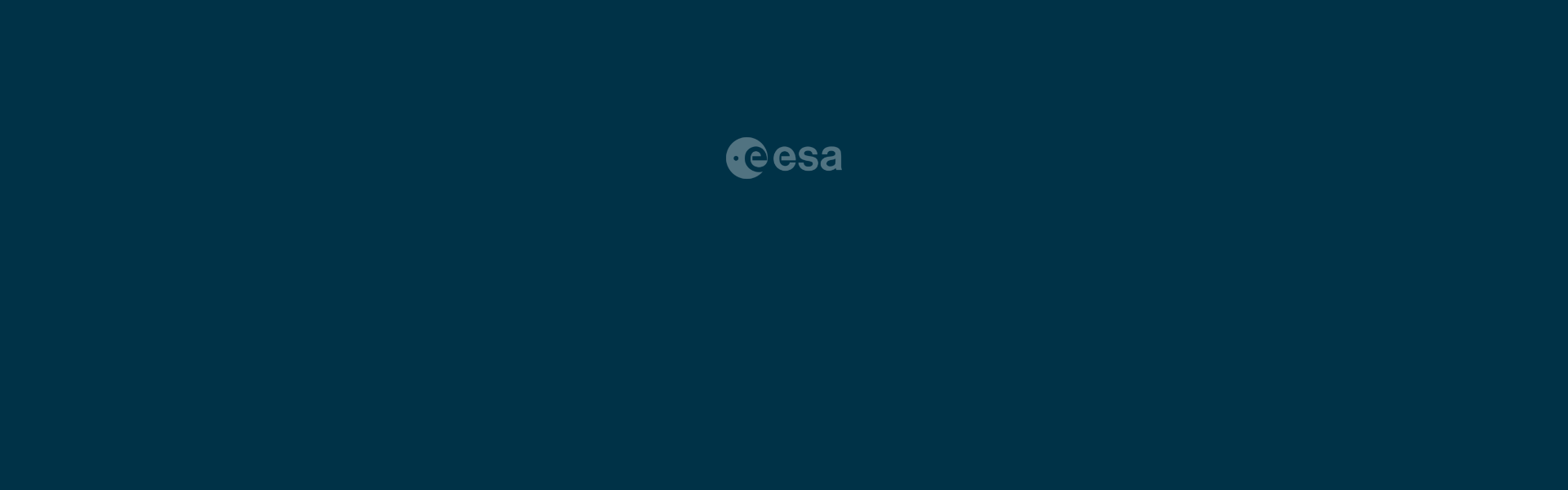
To evaluate the compatibility of next generation propellant systems manufactured using traditional and advanced welding techniques with new green propellants.
In 2011, Europe?s Registration Evaluation Authorisation and Restriction of Chemicals (REACH) added hydrazine to their candidate list of substances of very high concern. With this step, there is an associated risk that REACH will make hydrazine obsolescent (restrict or prohibit its use) in the near to mid term. While ESA is pursuing possible exemptions for hydrazine for space applications, additional risk mitigation is necessary. This additional mitigation includes development of green propulsion as a replacement for hydrazine and other high toxicity propellants along with the associated hardware. In recent years low toxicity (or ?green?) liquid rocket propellants (e. g. ADN, HAN, H2O2) have become attractive as possible substitutes for hydrazines and nitrogen oxides in low or medium thrust engines because of the reduced environmental impact and, more so, the cost savings associated with the drastic simplification of the required health and safety precautions.For the manufacturing of propellant systems, welding processes are commonly employed. Currently this is through the application of traditional joining methods such as TIG, Electron Beam, or Laser Beam welding processes. In addition to the traditional methods, advanced and ?greener? welding techniques such as solid state (e. g. Friction Stir Welding) welding are now considered as mature technologies and are being adopted by many manufacturing industries including automotive, ship building, and aerospace.Compatibility of the new ?green? most promising propellants shall be demonstrated w. r. t. the materials normally used for spacecraft and launchers propulsion systems manufacturing in pristine as well as welded conditions. In particular Stress-Corrosion Cracking behaviour of pre-cracked samples shall be investigated using the unique test methodology and test frames/cells developed by ESA.The proposed activity is divided into 3 tasks:1) The production of a number of pristine/welded coupons made from alloys (including Ti-6Al-4V STA and Annealed, Stainless Steel and Aluminium) and welding techniques (including Orbital TIG, EB Welding and Friction Stir Welding) identified from other ESA programs (it must be stressed that although this is not a welding development project, it will require the involvement of a welding manufacturing partner with experience with a wide range of processes including FSW).2) Testing of the pristine/welded coupons with the new green propellants using the unique test methodology and test frames/cells developed by ESA. This will require a partner capable of developing / handling the new green propellants.3) Evaluation of the pristine/welded coupons after contact with the new green propellants.