Demonstrator of parallel kinematics compliant mechanism for robotic exploration
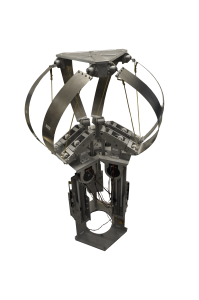
Develop a parallel kinematics mechanism with flexible elements for applications in robotic exploration with extended lifetime and robustness to collisions.
One current research in industrial robots is the development of mechanisms based on parallel kinematics, with flexible elements instead of rigid bars. This allows fast robots to operate close to humans or other robots, with reduced risk of damage in case of collision.Future robotic exploration will benefit from the advantages of parallel kinematics and flexibility of its elements, such advantages being notably:- For parallel kinematics: actuators can be placed inside the robot, hence protected from the environment. Actuators being a life-limiting element, their protection shall extend the lifetime of the mechanism.- For flexible parts: it would allow for fast working in an environment with other robots, humans, landers, hence making the mechanism robust to small collisions with obstacles, which are furthermore likely to happen in the early stage of autonomous robot operations.This activity is to produce the breadboard of a mechanism based on parallel kinematics with flexible elements.The end-effector to be placed at the mechanism will be determined by the specific application selected. The utilisation initially envisaged is grabbing and moving samples, similar to a Pick and Place application. The possibility to operate a 3D printer nozzle will be assessed during the applications identification early in the activity. 3D printing fits with the stiffness and speed properties of parallel kinematics, whereas sample gathering may fit better with the collision tolerance of flexible mechanisms. Choosing one or the other will therefore drive the design of the mechanism towards more stiffness or more flexibility. Regardless of the application, the mechanism shall be able to use conventional rotary actuators, hence not requiring the development of new actuators.The activity encompasses the following tasks:- Research the state of the art of parallel kinematics on ground,- Identification of potential applications (Moon resources utilization, Mars samples...),- Selection of target application; definition of requirements for accuracy, speed, stiffness and workspace,- Breadboard design. Selection of topology, materials and actuators,- Breadboard model production,- Testing to determine performances, robustness to collisions, identification of sources of position error.