Electron Beam Welding for Safety Critical Space Applications
Programme
GSTP
Programme Reference
G617-132QT
Prime Contractor
TWI LIMITED - THE WELDING INSTITUTE
Start Date
End Date
Status
Closed
Country
United Kingdom
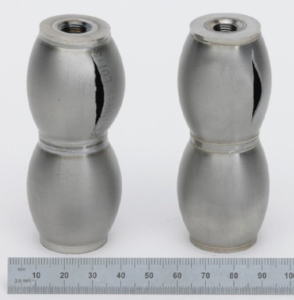
Objectives
To develop and adapt the Electron Beam Welding process for safety critical applications.
Description
The precision welding of metallic joints plays an important role in the production of components for space applications. In order to meet the demanding levels required, metallic joints must be produced which have the correct dimensional tolerance, are free from defects and exhibit the correct mechanical and corrosion performance. In particular, in propulsion systems all valves and pipes have welds which must be leak tight and prevent safety hazardous propellants from leaking. In recent years, there have been a significant amount of anomalies related to welding quality issues documented valves, and welding failures have jeopardised Space Projects Qualification activities and (in some cases) Missions causing substantial costs and delays.
It is therefore mandatory to develop and qualify welding methods which can consistently deliver the production of high quality defect free welds. One such technique is that of Electron Beam Welding (EBW) which is currently used in a number of safety critical applications in manufacturing sectors including Automotive, Nuclear and Aerospace. By developing and adapting such a technique for safety critical space applications, the costs and delays associated with welding failures will be significantly reduced, leading to improved confidence in users.
Since the EBW process is performed in a vacuum, shielding gases are not necessary, making the process particularly desirable for alloys such as Aluminium, Titanium, and Stainless Steels. For some difficult to weld materials such as Copper, and Molybdenum, EBW is the only acceptable welding method available. High welding speeds are possible with a low overall heat input resulting in low distortion. Furthermore, since there is the possibility to accurately manipulate the electron beam, intricate welding can be performed on very thin sheets (100 microns) or on small orbital welds, making this an ideal technique for applications such as safety critical flow control valves.
Industry is currently qualifying the methodology required to produce high quality reliable joints for Flow Control Valves. An existing design will be adopted and re- manufactured using the EBW process, and the results compared to the standard design which is currently welded using a Laser Beam welding process.
Application Domain
Generic Technologies
Technology Domain
24 - Materials and Manufacturing Processes
Competence Domain
2-Structures, Mechanisms, Materials, Thermal
Initial TRL
TRL 3
Target TRL
TRL 6
Achieved TRL
TRL 4
Public Document
Executive Summary