Producing inexpensive carbon-neutral steel from low-grade feedstock applying space In-Situ Resources Utilization paradigm
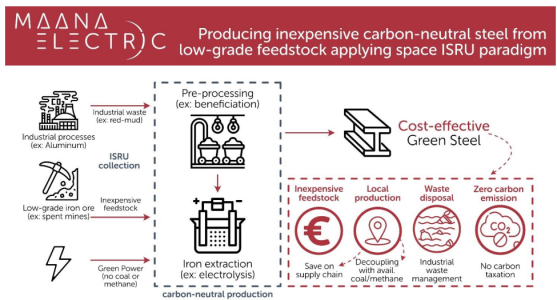
In the current global landscape, the escalating threat of global warming has become a paramount concern for the future of our planet, with carbon dioxide (CO2) emissions identified as a primary culprit. To counteract this looming crisis, significant efforts are underway among major political bodies to formulate legislation aimed at curbing emissions and steering the transition towards eco-friendly practices in the most impactful industrial processes. Notably, the steel industry emerges as a critical sector responsible for 5.7% of total EU greenhouse gas (GHG) emissions, making it a focal point for substantial reductions in both direct and indirect CO2 emissions.
The conventional method of steel production involves a high-temperature reaction of high-grade iron ores with carbon, resulting in the release of 1.8 tons of CO2 per ton of steel. The urgency to address this environmental challenge extends beyond merely identifying green iron production processes; it requires a holistic reevaluation of the entire value chain. The quest is not only for sustainable alternatives but also economically viable feedstock sources. In this transformative landscape, the paradigm of In Situ Resources Utilization (ISRU) methodologies comes to the forefront. Initially conceived for space exploration, ISRU technologies were designed to process unconventional feedstock, a principle now applied to terrestrial industries seeking sustainable solutions.
Recognizing the critical role of the steel industry in global dynamics, Maana Electric, a leader in ISRU technologies, is spearheading an initiative to apply the ISRU paradigm to iron production. Traditional iron extraction processes rely on high-grade iron-bearing minerals, which are depleting slowly. Maana Electric, therefore, explored alternative sources with lower-grade iron, investigating beneficiation techniques aligned with potential lunar ISRU architecture. Through a meticulous trade-off study, red mud, an unconventional feedstock containing iron, emerged as the most promising source.
In tandem, a second trade-off study identified Molten Oxide Electrolysis (MOE) as the optimal technique to integrate into an ISRU architecture for steel production. Subsequent experimental campaigns aimed to establish a Proof-of-Concept for iron extraction from red mud simulants using MOE. The initial phase revealed promising results, albeit with challenges related to the compatibility of materials for reaction containment and electrodes. To address these issues, a redesigned breadboard optimized for the process, incorporating a molten cathode made of copper, was developed and tested.
The conclusive testing campaign successfully demonstrated the extraction of iron from red mud using MOE. The use of a molten metal pool exhibited the highest potential for success, addressing scalability issues associated with electrode degradation and cost. However, challenges related to achieving and sustaining the high temperatures required for optimal MOE performance were evident. While technically validated, a comprehensive techno-economic analysis, informed by the experiments conducted, is imperative to assess the viability and scalability of the process and determine optimal operational conditions.
This groundbreaking initiative, a fusion of space-derived technologies and terrestrial industry needs, symbolizes a transformative step towards greener and more sustainable industrial practices. The collaborative efforts of Maana Electric and the innovative application of ISRU methodologies herald a new era in steel production, underscoring the potential for industries to align with environmental stewardship and drive positive change on a global scale.