Assessment of carbon ion engine technology targeting competitively improvement of electric propulsion for telecoms applications
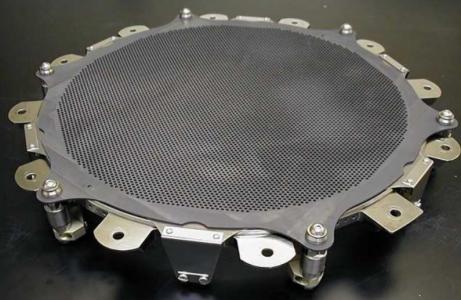
Starting from flight proven technology concepts, the design and demonstration of an Ion Engine in which all of the components exposed to plasma and involved in radiative cooling are fabricated from amorphous or carbon-carbon composite, to target the following objectives:- High thrust density resulting in increased thrust at lower operating temperatures.- Physically smaller thruster capable of delivering 150mN or more.- Lower dry mass (potential for at least 2kg saving).- Lower production costs for a carbon ion thruster, supporting lower mission prices.- Longer life screen grid to >25MNs (elimination of screen grid erosion as a life-limiting factor).- Simplification (mass price) of PPU design through improved thruster robustness/margins.
The 22cm gridded ion engines have already demonstrated that beam currents equivalent to a thrust level of up to 230mN can be extracted. This in turn requires a high plasma density within the discharge chamber to be produced. More recently however the limitations on thruster performance imposed by the Screen grid material and harness interface temperatures would prevent thrust levels in excess of 145mN from being considered without further a dedicated development programme.Building an ion engine in which all of the components exposed to plasma and involved in radiative cooling are fabricated from amorphous or carbon-carbon composite will address both of these current limitations. A carbon-carbon composite screen grid would dramatically increase the tolerance to grid erosion. An added benefit would be that the coefficient of thermal expansion of such a grid would be virtually zero and hence the increase in the grid spacing during thruster operations would be dramatically reduced. This will provide a higher grid perveance limit allowing even higher ion beam current densities to be extracted, and hence thrust levels to be produced (>230mN for a 22cm size device). Manufacturing the discharge chamber and external Earth-Screen from amorphous or carbon-carbon composite would both reduce mass and provide radiating surfaces with an inherent high emissivity. The high emissivity will reduce operating temperatures resulting in an engine design more tolerant to higher thrust densities. An added advantage would be that the thermo-optical properties of the external radiating surfaces would not be influenced by ground based facility interactions; i.e. the deposition of carbon sputter deposits from the facility ion beam targets would not change the thermo-optical properties. A corollary benefit of this approach would be the possibility of reducing the physical size of the engine. Currently 22cm Ion Thruster is perceived to be physically large and limits its potential use on smaller telecoms platforms and for other telecoms applications, in particular east-west station keeping. Designing an ion engine that is physically smaller but maintaining high thrust performance would allow the benefits of ion engines to be more fully exploited in the telecoms market. For example, the 145mN delivered by the existing 22cm thrusters could be achieved with a smaller thruster if it were scaled appropriately.Consequently, it is proposed to undertake a study that incorporates the following key activities:- Assess and implement the design of a 22cm sized carbon-carbon Screen grid, taking into account manufacturing/production processes and limitations imposed by the environmental (vibration) requirements.- Assess the performance of a standard (metal components) ion engine using a carbon-carbon screen grid.- Assess and implement the design of a 22cm sized carbon discharge chamber, anode, baffle and earth-screen, taking into account manufacturing/production processes and limitations imposed by the environmental (vibration) requirements.- Assess the performance of a ion engine (fitted with carbon-carbon screen grid) using components manufactured from carbon-carbon/amorphous carbon (discharge chamber, anode, baffle and cathode keeper) at higher thrusts (>200mN).- Preliminary assessment and scaling of a physically smaller gridded ion engine offering >150mN performance. The benefits of this study would be as follows:- High thrust density resulting in increased thrust at lower operating temperatures.- Physically smaller thruster capable of delivering 150mN or more.- Improved performance of grids (no differential expansion of carbon and screen grids since they are manufactured from the same material).- Lower dry mass (potential for at least 2kg saving).- Lower production costs for a carbon ion thruster, supporting lower mission prices.- Longer life screen grid to >25MNs (elimination of screen grid erosion as a life-limiting factor).- Trade-off between high thrust and high specific impulse: benefits for telecoms and science missions.- Trade-off between thruster and Power Processor Unit (PPU) performance; simplification of PPU design through improved thruster robustness/margins.