Development of a high performance microvibration isolation system
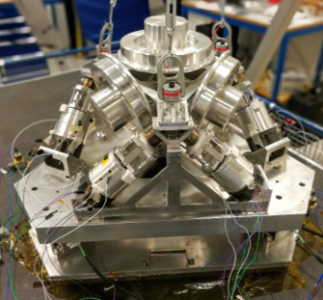
Mechanical disturbances drive system level choices on science missions. Drastic reduction of microdisturbances can simplify the spacecraft design and enable missions with more sensitive payloads. For example, high perfomance isolation systems for reaction wheels could avoid the need for hybrid AOCS system using expensive cold gass propulsion systems (ARIEL). The proposed technology should be suitable for all noise sources, or to isolate the sensitive payload itself. The isolation system should be high performance, low mass, low cost, low power, low complexity and versatile (tunable/scalable).
Typical isolation systems currently used are limited to passive isolators, based on viscoelastic elements. Other passive existing technologies include eddy-current dampers, the so-called D-struts and shunted piezo electric transducers. Active systems include voicecoil and piezo actuators and active eddy current dampers. This proposal is prompted by recent developments in the frame of TEC Technology Assessment supported work on electromagnetic shunt dampers connected to a negative resistance circuit showing promising performances. However, multiple promising competing technologies are under development in Europe and the TDA is open to all technologies fulfilling the following criteria:- Limited amplification of system resonances (~3dB)- 20 dB attenuation @ 20Hz, 50-60dB attenuation @ 100Hz, 80-90dB attenuation @ 200Hz . (Best existing systems provide 40dB @ 100Hz, but have not been flown.)- Low/predictable temperature dependence of isolation performance- Low complexity/ high reliability- Low mass, 25-75% of mass of isolated equipment- Low power consumption- Magnetically clean- Tunable/scaleble (to avoid complete system redesign as is currently the case for passive isolators)This activity aims to take the newest technologies demonstrated in the laboratory or via analysis and develop a full scale breadboard for one application (e.g. reaction wheel isolation). A typical configuration for these isolation systems is in the form of a hexapod, using 6 struts. The following tasks will be performed:- Selection of the application (e.g. reaction wheels, cryo coolers, payload isolation)- Design of a full-scale breadboard- Modelling and simulation/analysis of isolation system performance- Functional validation at strut level- Functional validation at hexapod level, including assessment of tunability