Magnetically Clean Reaction Wheel
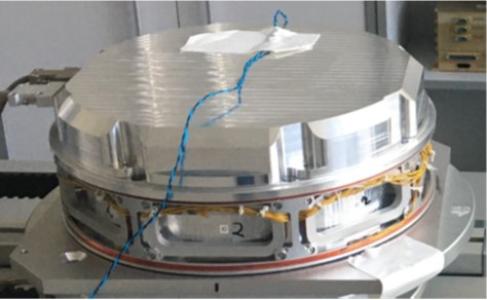
The main objective of this activity is to identify technologies and design options of a magnetically clean reaction wheel and to demonstrate its feasibility through the testing of an elegant breadboard.
Reaction wheels exhibit dominant magnetic field emissions that shall be reduced to allow the reaction wheel use on magnetically susceptible missions without negative impact on scientific objectives. Conventional reaction wheels use brushless DC motors with relatively high magnetic flux densities in large air gaps without any dedicated compensation or 'magnetic balancing' of the motor magnets. The motor external magnetic field together with contributions from further components, (ball bearings), combine to a significant magnetic dipole moment. Instruments to measure the magnetic fields are very sensitive to interference generated by the reaction wheels. With present designs, reaction wheels are either completely avoided in the spacecraft architecture (e.g. SWARM), or some degradation of the payload performances has to be accepted (e.g. Venus Express, BepiColombo or Solar Orbiter). Minimization of magnetic field effects may require fundamental internal design modifications with focus on the motor and parts made from ferromagnetic materials as primary contributors. The main configuration, the wheel drive electronics and especially spacecraft interfaces should preferably not be affected by such design modifications. With state-of-the-art magnetic system modelling and simulation software, the novel design options (reduction and/or compensation of magnetic sources, shielding, effectiveness of hardware 'de-perming', use of alternative materials, etc.) shall be studied and compared with the existing design status. Moreover, an optimisation of the magnetic design might also have positive effects on other parameters, e.g. reduction of air gaps in the magnetic circuit or reduction of eddy current induced losses, resulting in an increased efficiency and reduced power consumption. The implementation of the critical features in an early breadboard shall allow for preliminary testing and the necessary iterations. Finally, the improvements w.r.t. 'reduced magnetic signature' shall be demonstrated in a fully assembled elegant breadboard Model reaction wheel. The main steps of this activity are : 1) Review of the relevant missions and associated AC and DC magnetic requirements 2) Identify magnetic sources in existing space-qualified reaction wheels and summarize their overall magnetic performance. 3) Optimise magnetic design features using magnetic system modelling simulation software tools, and perform trade-off analysis regarding other performance parameters and environmental conditions. 4) Implement the novel design options in early sub-assembly breadboards and verify their effectiveness 5) Integrate the new/modified design features in an Elegant Breadboard Model reaction wheel 6) Test the magnetic characteristics of the Elegant Breadboard Model before and after environmental testing 7) Verification of the effectiveness of any reaction wheel level treatments and that of any specific precautions during typical AIT activities including transport and storage. This shall include a mapping/inventory of potential sources that may lead to a re-magnetisation and any other inadvertent degradation of the magnetic signature 8) Critical review of the results and compliance with the requirements, elaboration of a development plan