Electrospray colloid electric propulsion system development
Programme
GSTP
Programme Reference
G617-190MP
Prime Contractor
Queen Mary University of London
Start Date
End Date
Status
Closed
Country
United Kingdom
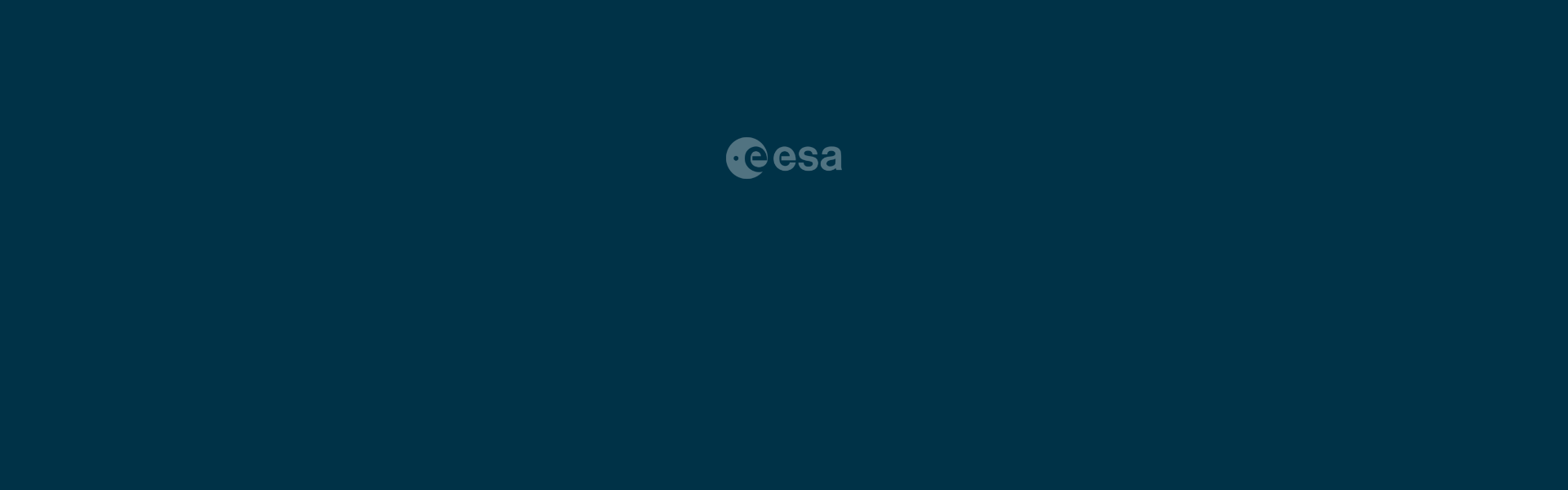
Objectives
The objectives of this activity are to improve the specific impulse, thrust density and reliability of the existing micro-colloid thruster technology by the application of mass production manufacturing techniques developed for terrestrial electrospray applications, e.g. inkjet printers. If successful these techniques will also dramatically reduce the recurring costs of the thruster technology.
The activity will initially concentrate on the thrust head technology design modifications and manufacturing process development, culminating in the manufacture and experimental performance validation of a high thrust density Colloid Thrust Head breadboard model. After initial performance verification the long term compatibility of thrust head components will be demonstrated via endurance testing. The activity will conclude with the design definition of the microfluidic system (including propellant storage and supply) and the power supply and control system (including feedback control of thrust) required for the development of a complete Colloid Thruster System.
Description
Development of electrospray colloid electric propulsion (EP) has been underway since 1999. Active research in this field has been pursued because it offers the possibility of a low cost, low W/mN, high SI, low dry mass system combined with a scalable high thrust density capability. To date these development programs have resulted in breadboard thruster concepts designed around MEMS manufacturing techniques, achieving TRL3 maturity with demonstrated specific impulse and specific power performance levels comparable to Hall effect (HET) and gridded ion engines (GIE). The MEMS processes are however time consuming (expensive) and result in relatively low colloid emitter densities and therefore low thrust levels. The design of the emitters and extraction electrodes are also constrained by the MEMS processes which have resulted in relatively poor reliability due to shortcircuiting of the extraction electrodes by the electrically conductive propellant, referred to as 'liquid bridging'. As a result, the practical application of this technology has to date been limited to future mini and CubeSat missions requiring very low thrust and low total impulse levels.
The use of manufacturing techniques developed for terrestrial electro-spray applications such as ink-jet printers (originally a spin-off of space colloid thruster development activities) would if successful eliminate the need for MEMS fabrication, enable an order of magnitude increase in the colloid emitter packing density whilst also eliminating the possibility of fluid-bridging due to the encapsulated design of the extraction electrodes. Access to this manufacturing technology is therefore the key step required to make the colloid thruster concept truly low cost with an anticipated performance of 0.3mN/cm2 at an Isp of up to 3000s. This compares favorably with the state of the art GIE technology on BepiColombo which operates at 0.4mN/cm2 and therefore offers the possibility of the technology eventually being applicable to larger commercial platforms.
The proposed programme consists of the following 4 tasks.
- To identify a baseline Colloid Thrust Head Model design. Within this task a thruster performance requirement shall be derived in conjunction with the Agency. Based on this specification a new design approach shall be identified concurrently with the definition of an appropriate low cost manufacturing methodology.
- To identify a low cost manufacturing route for construction and manufacture of thrust head components and any design variants. Within this task all components (breadboard thrusters, ground support equipment) necessary for the test programme shall be manufactured and procured. At the end of this task the output will be an assembled BBM Colloid Thrust Head Model and setup test facility.
- To validate the design methodology experimentally. This task is an experimental evaluation of the Colloid Thrust Head model and any design variants identified (using laboratory power supplies) to validate the underlying design methodology is able to meet specified operational characteristics. In particular it should verify that previous failure mechanisms have been overcome by the design methodology adopted (including an endurance test of TBD hrs).
- To identify a road-map for the future development of the concept thruster into a TRL 6 system. The object of this work task is to produce a definition of a Colloid Thruster System based upon the results of the Colloid Thrust Head Model testing and overall system design clearly outlining the roadmap for the development.
Application Domain
Generic Technologies
Technology Domain
19 - Propulsion
Competence Domain
7-Propulsion, Space Transportation and Re-entry Vehicles
Initial TRL
TRL 3
Target TRL
TRL 4
Public Document
Executive Summary