High Speed Deterministic Polishing of Strongly Aspherical Mirrors
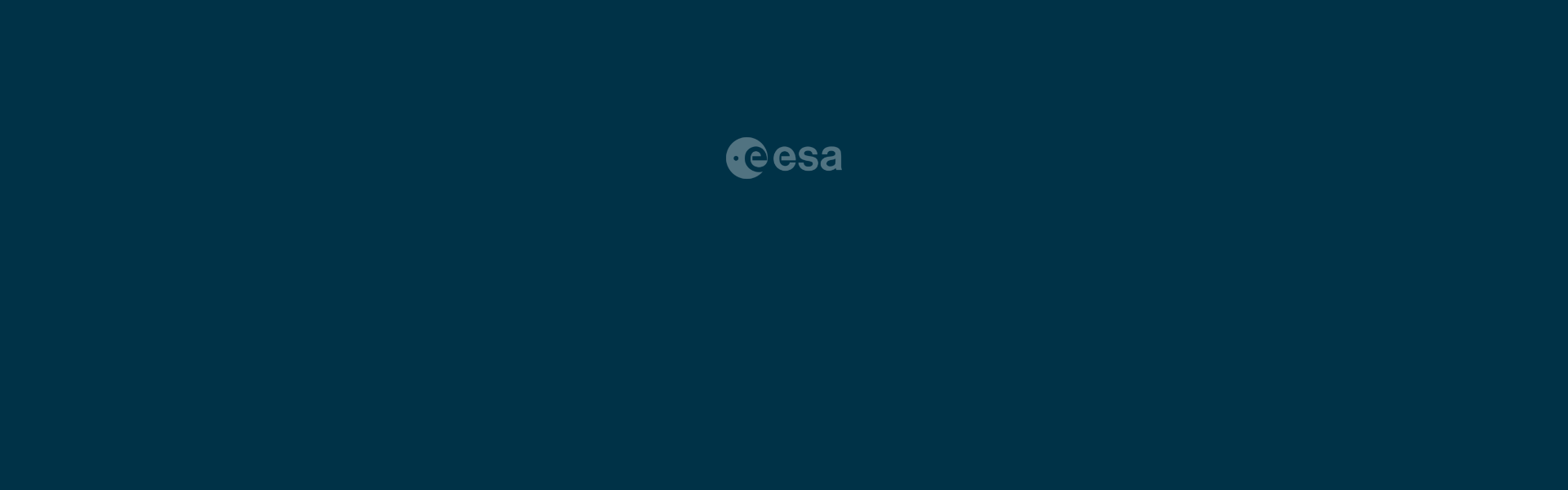
The activity was able to develop and improve technologies and processes (such as polishing) that will enable manufacture and production of lightweight, highly aspherical, metallic optical mirrors with the accurate surface shape and low roughness needed for high performance optical systems, such as telescopes and high-resolution spectrometers.
These designs have been increasingly investigated in the build of compact, lightweight and high performance space-based instruments. But the effort and time needed to polish these mirrors to meet the requirements for highly-detailed space instruments has meant their reliability has been hard to predict. This has led to uncertainty in lead time and cost. Now, advances in melt-spinning technology, the development of new aluminum alloys and changes to manufacturing methods for metallic mirrors manufacturing has opened new possibilities for fully-metallic instruments with challenging designs
These developments mean instruments such as compact spectrometers, large field-of-view telescopes or relay systems, could be developed using only metallic materials, making them better able to withstand cryogenic temperatures.
The activity studied different materials and ways of polishing them to understand how best to manufacture these mirrors. Eventually, lightweight mirrors of 10cm square and 20cm by 10cm were made using an aluminium alloy, AlSi40, plated with NickelPhosphorous, and their structure and longetivity evaluated through a test campaign.
The largest mirrors survived the thermal and vacuum cycling tests before the performance of the mirror in cryogenic conditions was evaluated, using real-time monitoring of the surface error as the mirror was subjected to temperatures ranging from 295 to 200 Kelvin.The activity was able to successfully develop two mirrors that met the strict requirements of optical instruments.