Magneto-resistive angular sensors for space applications
Programme
GSTP
Programme Reference
G617-180MS
Prime Contractor
RUAG Space Germany GmbH
Start Date
End Date
Status
Closed
Country
Germany
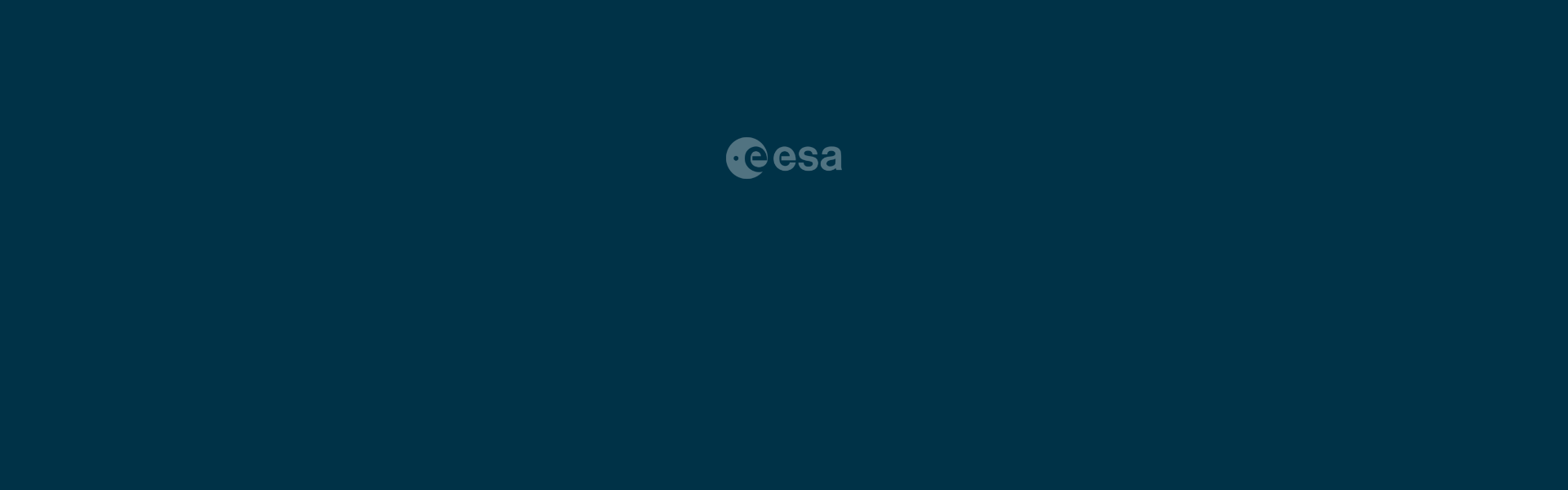
Objectives
The objective of this activity to design, manufacture and test an engineering qualification model of a position angular sensor based in magneto-resistive angular technology. The sensor to be developed may be used for a wide range of applications including instrument mechanisms (Earth Observation or science missions), antenna pointing mechanisms and other mechanism applications such as solar array drive mechanisms or reaction wheels.
Description
The magneto-resistive sensor technology developed in Europe is used for many industrial applications and several Mars robotic exploration missions. However, the sensor solution using this technology has been developed and qualified for space outside Europe. Several potential users of the technology in Europe are interested to use the technology for mainly their specific mechanism related needs and also robotic system related needs. The application or service domains are multiple including Earth Observation, Space Science and Robotic Exploration.
Given the strong interest from European users, a TRP Technology Assessment Study was performed (TSS13-04SB, Magneto-Resistive Sensors for Space Applications) to analysis the needs, collect technical requirements and to derive a potential designs that could satisfy various needs.
The proposed solution is an incremental off-axis position sensor based on Anisotropic Magnetoresistive Effect (AMR) sensors with an optional index pulse. It forms the basic version of magneto-resistive sensors and features a very simple, yet robust, compact and lightweight setup comprising only low signal conditioning efforts and straight-forward front-end electronics. The technology offer also other advantages like the wide temperature range tolerance, radiation hardness, good tolerance to air gaps and to shaft eccentricity or reliability.
The concept is a cost-effective and contactless solution with a medium resolution/accuracy performance that provides an alternative to the low performance potentiometers. Optical encoders offer a higher performance solution but are costly and more complex.
The five tasks, or development steps, defined for the activity, are:
- Preliminary Design and Breadboard Testing.
- EQM Design.
- EQM Manufacturing, Assembly and Integration.
- Qualification Testing.
- Synthesis Activities.
Application Domain
Generic Technologies
Technology Domain
15 - Mechanisms
Competence Domain
2-Structures, Mechanisms, Materials, Thermal
Initial TRL
TRL 3
Target TRL
TRL 6
Achieved TRL
TRL 6
Public Document
Executive Summary