Small, Inflatable, High Pressure Composite Tanks for Human Spaceflight
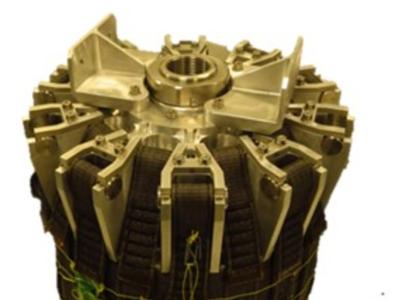
The primary focus of this project is to develop demonstrator gas and liquid storage solutions for long duration, manned missions, that optimize mass and volume whilst satisfying safety and design requirements.
One of the issues facing the development of manned, long duration space missions is how to manage liquids/gases for life support. Gases such as O2, CO2, CH4 etc are inputs and by-products of life support systems, for non-regenerative (open-loop) systems. Stores should be enough to sustain any short duration crew visit and until regenerating (closed loop) systems can be installed. - The use of fibre reinforced composites to manufacture single shell, high pressure tanks for liquids and gases is known in other industries (e.g for heating, storage in transport or automotive applications, Natural gas tank or Hydrogen gas tanks working at upto 700bar with upto 2000 Litre capacity). - Composites tanks are recyclable and filament wound structures offer superior impact resistance, corrosion resistance and fatigue/vibration characteristics to metallic solutions. - Many known polymer and fibre combinations can be used and with proper design can be tailored to leak before burst for safety, as well as other operational requirements. Hence composites offer cheaper, smaller and lightweight solutions compared to metallics or other materials.- Polymers such as Thermoplastics are also favourable for cryogenic applications, which would enable low temperature cooled storage of higher pressure liquids in lower volume.- For flexible and inflatable tanks a dry fibre, filament wound and stitched shell with flexible lining may be adapted for a flexible, high pressure storage solution (e.g.50-100bar).This activity includes a review of existing composite storage tank solutions and select existing candidate materials and manufactured designs for space applications. If necessary, these materials will be characterized for space applications and then a prototype tank will be manufactured with the selected manufacture process. The demonstrator tanks shall be designed to satisfy the following requirements: 1) optimise mass and volume for a given stored gas/liquid2) should exhibit sufficient safety and reliability in appropriate mission conditions over the mission life.3) should provide gas at 1 bar pressure even if the storage pressure is higherThe performance of the demonstrator tank shall be determined by experimental test using mechanical load plus pressurization to establish maximum design loads and then followed by appropriate over-pressure to demonstrate sustained output capability of 1 bar pressure. Final test is over pressure to rupture (demonstrating the target failure mode of leak before burst).