Paving the road for large area sintering of regolith
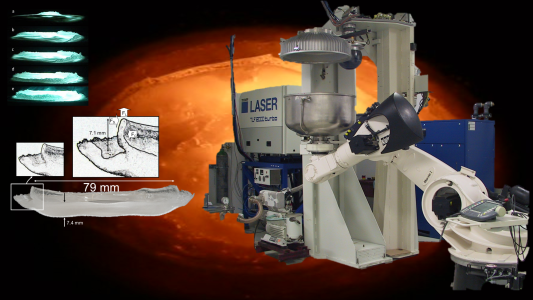
Lunar regolith can be sintered/melted by intensive solar or laser radiation to dense and rigid structures. For reaching the required energy densities, sunlight can be focused by means of mirrors or lenses. In the present study, solar radiation is simulated by a CO2 laser system, providing a maximum power output of 12 kW cw. The laser has been used to generate large laser spots of 50 mm respectively 100 mm. In both cases a parallel laser beam with the same diameter of the laser spot has been generated to make the spot diameter independent of the distance to the target powder. A major concern of the study is the productivity in consolidating surface areas and the quality of the sintered material. Important quality measures are the density and the mechanical strength as well as the smoothness and the uniformity of the consolidated layer. Regolith is not simply compacted to arbitrary geometries when locally annealed by intensive light. A rapid densification of the generally fluffy powders is associated with melting and viscous flow resulting in a significant deformation of initially homogeneous powder beds. Light focused to small spots can be used for obtaining parts with good geometrical definition, but productivity is generally low and, driven by surface tension, single drops or islands of molten material might be formed. Large spots instead form a pool of molten material which follows the laser spot to form tracks of sintered or molten material. Different geometries have been evaluated to form parts with interlocking capabilities. In the focus interest have been simple 2D structures which can be used to pave areas used as landing pads or streets. The laser sintering has been performed directly in the powder bed of EAC-1A lunar regolith simulant. Maximum sintering/melting depth reached in this study has been 25 mm with 100 mm diameter laser spot and 10 kW laser power output for 40 minutes annealing time at one position. 20 mm sintering/melting depth has already been reached at laser power outputs between 9 and 11 kW for 20 minutes. Applying vacuum does not change the sintering kinetics and the parts quality significantly. Moving the laser spot (both: 50 and 100 mm spot size) at a speed of 5 mm/min relative to the powder bed surface results in consolidated tracks without cracks formed in the consolidated glassy/crystalline material. Higher speeds generally result in a cracking of the consolidated material. Compressive strength of the material is about 100 MPa, which however shows a large scatter between 50 and 220 MPa due to residual internal stress and an inhomogeneous microstructure: towards the surface which has received laser light the material is glassy while the material tends to crystalize in deeper layers. With an optimal 2D structure considering all requirements for the laser track, such as, speed below 5 mm/min, no overlapping tracks and interlocking capabilities, parts have been generated, size ca. 200 x 200 mm and a weight of ca. 1 kg. With a recoating unit, parts consisting of multiple layers have been generated. Internal thermals stresses, however, result in a severe cracking.