3D printing of a model building block for a lunar base outer shell
Programme
GSTP
Programme Reference
G617-153QT
Prime Contractor
DLR - German Aerospace Center
Start Date
End Date
Status
Closed
Country
Germany
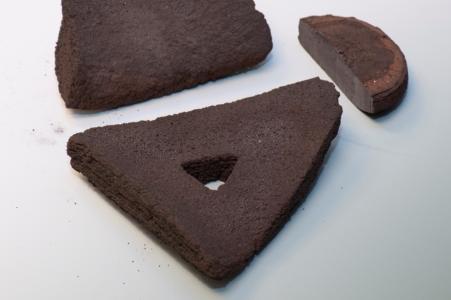
Objectives
The project aims at developing a 3D-printing process by fusing/melting/sintering (model) lunar soil material with the use of concentrated solar energy. The intended first result is a brick-size model building block of a lunar base outer shell.
The project will study various parameters of the production process as well as of the model lunar soil in order to better understand and optimise the overall process also in view of application on the Moon.
Description
The proposed project is a direct continuation of the ESA - GSP project ?3D printing of a lunar habitation?. A similar project called ?SinterHab - 3D printed moon concept? was presented by NASA and the international space university almost at the same time (http://www.a-etc.net/sinterhab/).
Both projects analysed and proved an economical design concept for a human- rated Moon-base that foresees an inflatable inner structure, which is protected by an outer shell that is self-supported and provides protection against spaceradiation and meteoroid impacts. In order to reduce the amount of material transported to the Moon, the concepts envisaged to produce such an outer shell by using material from the Moon and to ?print? building blocks of such a shell by using a 3D printing process.
While the ESA GSP concept relied on a binding agent for the printing process (requiring an unwanted additional mass transport from earth to moon for such a binder), the NASA concept focused on a micro-sintering process for transforming the loose lunar regolith into a solid structure. The energy for this sintering is derived from electricity powered by solar panels.
The project proposed below distinguishes itself from above 2 projects in the physical process of binding the lunar dust particles: It is proposed to investigate the feasibility of 3D printing by using directly the heat from the sun, concentrating the sun-rays within a solar furnace to directly sinter lunar soil. (Such a solar furnace promises higher efficiency than the before mentioned methods and could have a secondary use after the construction of the base is finished. Solar furnaces are also applied for production of hydrogen, another important topic for a lunar outpost.).
The European Astronaut Centre (EAC) is highly interested in applying the developed know how in a follow on project to establish at EAC a representativemodel of a lunar base in real size for demonstration and astronaut training purposes.
The activity will cover the following tasks:
- Identification and provision of representative ?lunar? material (taking heritage from the GSP project).
- Assessment of the feasibility of fusing/melting/sintering this material in thesolar furnace with the objective to finally produce a brick-size block ? Identification of (potential) interim steps and necessary processes and equipment (e.g. a sample moving device that allows a 3D layered printing).
- Performing the fusing/melting/sintering process (in a first step static, then 3D by use of a moving device).
- Analysis of material properties of the fused/melted/sintered material.
- Analysis of the robustness of the fusing/melting/sintering process with respect to parameters such as rheological, mechanical, chemical, electrostatic properties of the soil.
- Analysis of the production process in order to identify ways and means to influence and optimize process performance (speed, energy consumption,precision), material properties (consistency, mechanical properties), and block shape (degree of shape detail).
- Identification of elements and modifications that would be necessary to perform such a brick production on the Moon, as well as identification of related requirements for a Moon-based process and related equipment.
The proposed additional work is intended to support the development of the solar
oven equipment to allow printing in the z-direction ? which is essential for brick manufacturing ? to allow further characterization of the regolith simulant materials for comparison with actual lunar soil and to enable the fabrication of several brick
demonstrators.
The development of the solar oven equipment will involve the fabrication of a 3-axis table to allow sintering of successive layers of lunar regolith i.e. printing in the
vertical direction. Ongoing work has successfully demonstrated feasibility of the sintering process in the x-y plan. Sintering in the z-direction is key for the manufacturing of lunar base building blocks. Moreover the 3-axis table will provide
additional flexibility and precision in the regolith deposition and sintering process and resulting improvement of the quality of the sintered regolith material.
Additional characterization of the regolith simulant (e.g. by X-ray diffraction at varying temperatures) will be beneficial to deepen the understanding of the base material and the potential differences with the actual lunar regolith. This is key for scoping the potential modifications required for the actual application of the developed solar energy sintering process in the actual lunar environment. Aspects to assess will include the glass phase content of the simulants (as compared to the actual lunar soil) and the structural changes occurring in the regolith formed during
sintering.
It is also proposed the fabrication of additional brick demonstrators to be exposed at several ESA sites (EAC, ESTEC) and at the contractor?s premises.
Application Domain
Generic Technologies
Technology Domain
24 - Materials and Manufacturing Processes
Competence Domain
2-Structures, Mechanisms, Materials, Thermal
Initial TRL
TRL 3
Target TRL
TRL 5
Achieved TRL
TRL 4
Public Document