De-risk assessment: Prediction of life time of soldered electronic assemblies for space, based on thermo- mechanical simulations
Programme
GSTP
Programme Reference
G617-241TAfp
Prime Contractor
IMEC VZW. Interuniversitair Micro-Electronica Centrum VZW
Start Date
End Date
Status
Closed
Country
Belgium
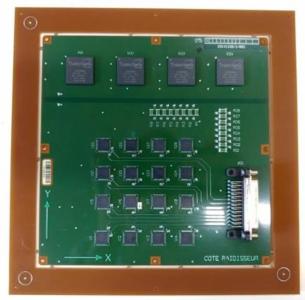
Objectives
•To investigate on a simulation method, based on state-of-the-art Finite Element Modelling (FEM) tool, to be able to predict or to give a confidence indicator on the thermo-mechanical reliability of solder joints of assembled packages
•Validate the ‘cycles to failure’ predictions with thermal cycling tests on daisy chain components soldered on different printed circuit board types
Description
Background and justification:
•Solder joint failures is one of the main failure mechanisms determined after thermal cycling qualification testing for space (ECSS-Q-ST-70-04C)
•The lifetime prediction of solder joints of components is crucial for TAS-B. A large range of new power units are under development and will address different types of missions: LEO, MEO or GEO, corresponding to large number of equivalent thermal cycles. This equipment will embed a lot of components of the shelf (COTS) and internally developed components, packaged in plastic BGA (Ball Grid Array).
Achievements and status:
•A simulation methodology is developed which allows to predict the lifetime of component assemblies soldered with eutectic SnPb. The core of this methodology is the empirical model translating the output from simulation into number of cycles to failure.
•A test structure is designed and procured allowing for thermal cycling testing of BGA, QFN and chip resistors. Three printed circuit board structures are used.
•Simulation is performed on the test structures and cycles to failures are predicted.
•2000 thermal cycles are performed on the test structures. Resistances are monitored. Failure analysis is performed to identify the fractures in the solder joints.
•We can conclude that the life time predictions for QFN and BGA are within the target (±25%), while chip resistors are substantially underestimated with respect to cycles to failure. The models could well indicate where solder cracks are occurring and also well estimate the effect of different board material and structures.
Benefits:
•The simulation approach allows for making predictions in design phase, and before any prototype is procured and tested. If the model indicates a life time below the qualification requirements, the design can be adapted, or a different component can be selected. Modifications in design phase cost typically 10 times less than during prototype phase. This virtual qualication approach also contributes to “first time, right design” achievement.
Application Domain
Generic Technologies
Technology Domain
23 - Electrical, Electronic and Electro-mechanical (EEE) Components and Quality
Competence Domain
2-Structures, Mechanisms, Materials, Thermal
Initial TRL
TRL 3
Target TRL
TRL 5
Achieved TRL
TRL 5
Public Document
Executive Summary