Nozzle Manufacturing using Metal Spinning
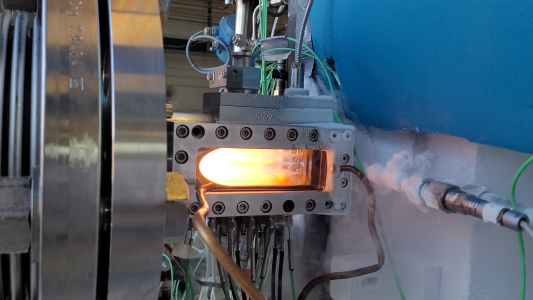
The objective of this manufacturing demonstrator project is to develop cost effective manufacturing processes for metallic nozzle extensions using metal spinning. The objective of this activity is the manufacturing and verification of at least two full scale samples made of Carpenter 21-6-9: one inner nozzle shell and one outer nozzle shell.
The previous GSTP de-risk activity has demonstrated the manufacturing feasibility of an inner nozzle shell. A full size inner part has been produced in 253MA Stainless Steel and a subscale part in Carpenter 21-6-9 Stainless Steel.
The main benefits of this manufacturing process are a potential recurring cost and lead time reduction for the nozzle extension (since the number of parts, welds and other manufacturing steps required for the nozzle manufacturing would significantly decrease).
The manufacturing process shall be compatible with the sandwich nozzle manufacturing in use for the current launcher nozzle designs, which comprise an inner nozzle into which channels have been milled to which a thinner outer is welded.
The main tasks for the activity object of this proposal are the following:
1. Produce a full scale Carpenter SS-21-6-9 inner nozzle shell. This includes:
-
procuring the Carpenter material
-
conducting short term trials with 253MA material to establish feasibility of spinning in air (thus allowing cost reduction by eliminating the need for a second mandrel)
-
feasibility study to establish whether the spin lathe machining tolerances are adequate for achieving GKN requirements for uniform part thickness.
-
developing thin wall machining fixtures (inside and outside) to produce a conforming inner nozzle part on the assumption in line machining is not possible.
2. Produce a full scale Carpenter SS-21-6-9 outer nozzle shell. The intention is to establish the feasibility of producing an outer part which will "match" an inner, the outer being significantly thinner than the outer. This includes:
-
Spin an outer shell over the existing inner mandrel and compare the conformity of the part to the inner shells already spun. This will establish how close a fit is possible from a spun only part.
-
Conduct initial trials to establish the feasibility of spinning outer shells over the previously manufactured inner shell. If the feasibility of this process is demonstrated, this would represent an additional recurring cost reduction driver for the nozzle extension.
Perform dimensional and mechanical verification on the manufactured nozzle parts.
It is proposed to change the budget, scope and the duration of this activity.
Additional applications cases were identified expanding beyond the originally identified time scale, thus leading to the proposed enlarged scope, budget and duration in order to address the full range of applications.
The goals of the proposed change are: to identify and apply different options for post welding and forming heat treatment on metallurgical profiles, test of high strength nickel alloys such as Inconel 718, use of thinner and commercially available Carpenter 21-6-9 material, analyse the effects on the inner cone of spin forming the outer cone over the inner cone and the geometry control achievable for the outer and inner pair of nozzle cones.
In particular, additional details have been added to point 3 of the original description of the activity. The change aims to build on the knowledge acquired in the production of the full scale Carpenter SS-21-6-9 outer nozzle shell. One step forming process, segments of material are cut from flat sheet and rolled and welded to create a cone or straight tube preform component. These would then be spin formed into a subscale nozzle component of the scale 900-1200mm inside diameter x 300mm deep in Carpenter 21-6-9. The purpose is to explore the potential benefits on metallurgy, profile conformance, process efficiency and material utilisation of starting from a tube and cone preform.