Survey PCB techniques for high dissipative components
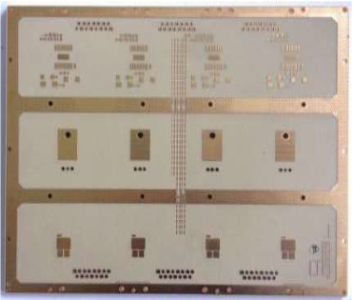
Main objective are:-Survey of terrestrial best practices to mount dissipative components directly on PCBs and heat transfer methods to baseplate.-Selection of most promising approaches checking their applicability for space apps.-Test verification of most promising methods.
In terrestrial electronics, a number of technological solutions have been developed and verified to allow direct (power) SMD EEE components mounting on PCBs with very good thermal conduction properties to the applicable thermal sink/baseplate.There are different principles (from rather basic - Insulated Thermal Substrates to Filled Thermal Vias, combination of Microvias and Buried Vias - to advanced approaches - including micro heat pipes embedded in PCBs).See for example the information provided at the following web links:a. http://www.we-online.de/web/en/leiterplatten/webinare/archiv/waermemana…. http://www.bergquistcompany.com/thermal_substrates/t-clad-product-overv…. http://doc.utwente.nl/77481/1/advances_in_integrated.pdfThe interest in this activity is not only due to the reduction of the thermal path from power component to thermal sink (a reduction of the relevant thermal resistance by a factor 2 allows to use the same device to 2 times the original dissipated power), but also:1. outstanding reduction in manufacturing costs due to full automated SMD mounting (also for power devices), without the efforts in design, layout, manufacturing and control of mounting through-hole packages to structure (stiffeners, etc - see example b. above);2. likely optimal control of CTE mismatch also for large SMD packages (see example a. above).Plan of work:1. Survey of terrestrial best practices to mount dissipative components directly on PCBs and heat transfer methods to baseplate.2. Selection of most promising approaches checking their applicability for space apps.3. Test verification of most promising methods.The activity is proposed by TEC-EPM (leading technical officer, ensuring the application/system level view); substantial expert support and contribution is expected from TEC-QTM and TEC-QTC, to cover space feasibility and material/component engineering aspects.