Verification methodology for parts made by AdditiveManufacturing
Programme
GSTP
Programme Reference
G61C-008QT
Prime Contractor
AIRBUS DEFENCE AND SPACE SAS
Start Date
End Date
Status
Closed
Country
France
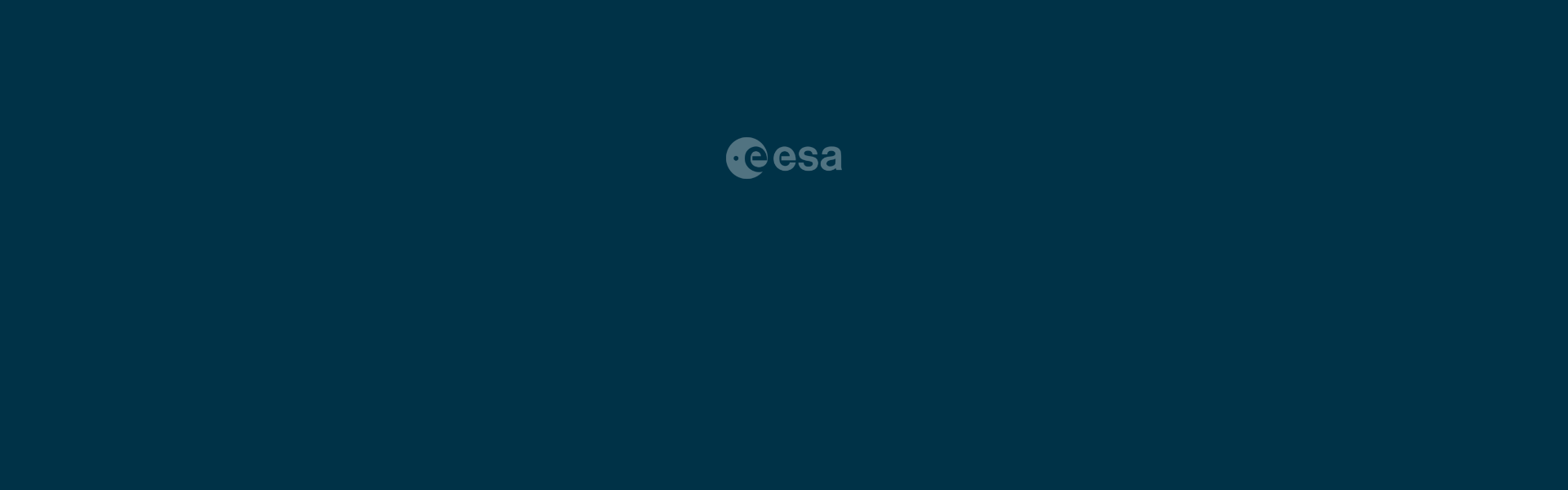
Objectives
The first objective is to establish the capability of various Additive Manufacturing (AM) suppliers in Europe to produce space hardware. The second objective is to establish a qualification route applicable to AM produced item ? validating a process and/or a part manufactured by a process.
Description
The activity is to be carried out by a consortium comprising several AM suppliers, using the same test house in order to ensure consistency and similarity of all the tests conducted. Ideally, the prime contractor should be a Large System Integrator (LSI), but could also be an equipment or a Tier 1 supplier, i.e. a company having design and testing capabilities (or the capability to establish test plans).
The Prime contractor will define what needs to be provided, as well as which verification means are required together with the part (e.g. all samples for assessing material characteristics). The Prime contractor will indeed provide to the consortium a promising metallic part to be redesigned and manufactured using AM process in combination with pre and post processes. It will also provide the specifications and the requirements of the part. The trade-offs leading to the selection of the potential parts to be redesigned and leading to the selection of AM suppliers shall be duly explained.
The design of the part shall be optimized to take advantage of the AM process capabilities. The design shall be based on material properties provided by the identified AM supplier. The part designed shall include advanced features e.g. thin and thick sections, buried cavities, trabecular structures. The design shall be submitted to typically 3 to 5 ? depending on the complexity and cost of selected part and associated test costs ? AM suppliers.
The AM suppliers shall at least provide:
- The powder characteristics (shape, grain size distribution, flowability, humidity percentage).
- The laser parameters (power, scanning speed?).
- The scanning strategy.
- The building orientation and the supporting structure strategy.
- The in-process samples to be made in the build job together with the bracket to be produced.
- The post process performed on the bracket (e.g. sand blasting, polishing, machining, heat treatment, HiPing?).
The consortium shall define a verification strategy and qualification route with inputs from the Prime contractor. A test plan should be drafted to characterise the in processed samples and the parts produced. The test plan shall be agreed by ESA.
The capability to detect defaults using conventional NDI (Non Destructive Inspection) techniques shall be investigated on as processed items and, when feasible, repeated on the same items after surface finishing. In addition, mechanical tests will be performed on samples containing defects to quantify knock-down factors and physical destructive analysis will be performed to correlate the population of defects detected on as processed and on finished items with the mechanical characteristics.
Guidelines will then be proposed for verification methods of ALM manufactured
items.
The main tasks of the activity will be:
- Task 1: re-design for Additive manufacturing of the part selected.
- Task 2: manufacturing preparation and testing strategy.
- Task 3: test campaign on the items produced.
- Task 4: comparison of the test results.
Application Domain
Generic Technologies
Technology Domain
24 - Materials and Manufacturing Processes
Competence Domain
2-Structures, Mechanisms, Materials, Thermal
Keywords
32-Clean Space
Initial TRL
TRL 3
Target TRL
TRL 5
Achieved TRL
TRL N/A