Damping behaviour in AM material based parts
Programme
GSTP
Programme Reference
GT1A-007MS
Prime Contractor
SPACE STRUCTURES GMBH
Start Date
End Date
Status
Closed
Country
Germany
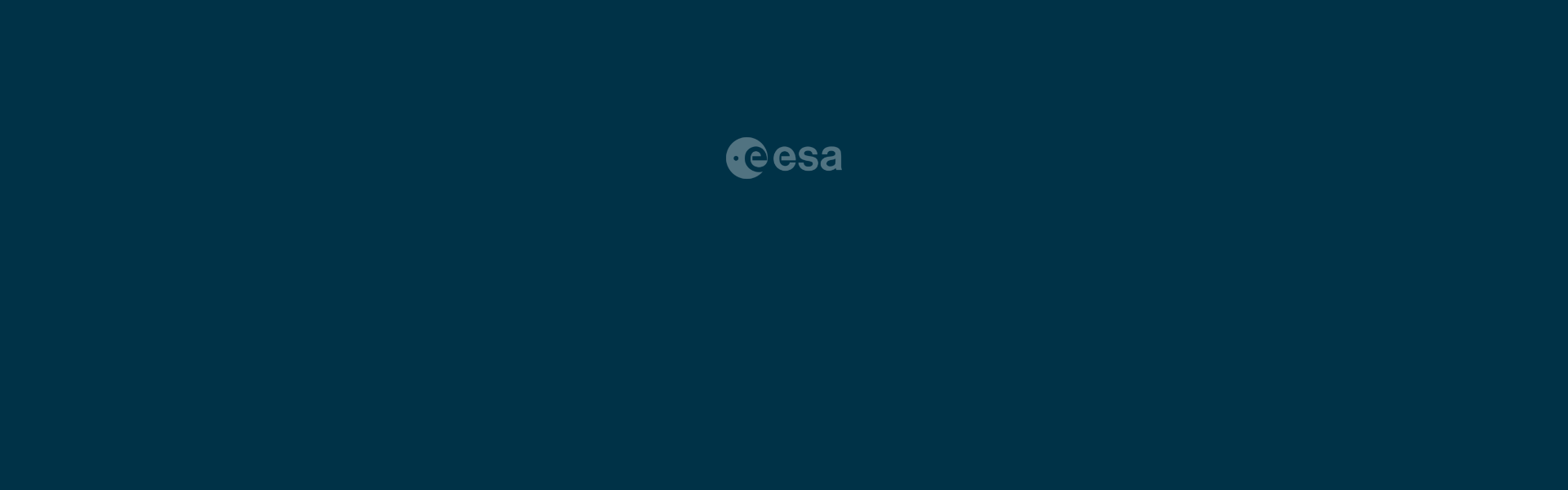
Objectives
The objectives of this activity are to assess the damping characteristics of AM materials and to simulate and predict damping behaviour of AM materials, thus improving the design of vibration sensitive parts..
Description
Vibration is one of the main issues when it comes to the design of space hardware and as such, it should be considered in the early phases of spacecraft design. When this factor is overlooked, a later identification of vibration and shock issues causes a deep impact on the performance of the spacecraft. Often the only solutions available, such as a dedicated damper, are detrimental for design, cost and schedule of the mission.
;
Therefore, the knowledge on damping characteristics of materials and parts is essential to guarantee the adequate performance from the design phase. In a previous GSTP Activity ?Assessing the use of Advanced Manufacturing to improve and expand space hardware capabilities?, the use of additive manufacturing to produce damped solutions in a single step was tested. This was achieved by using the raw material (metal powder) as damping agent. It was demonstrated that such particle-damped solution could increase by 200% and to up to 1400% vibration damping, when compared to CNC milled metal parts.
;
However, the large freedom of design and manufacturing parameters requires an appropriate prediction model to develop designs effectively. As such, the objective is to employ numerical simulation technology e.g. discrete element method (DEM) to develop prediction models as enabling design tools.
;
This activity intends to take benefit of the achievements of the former activity to enlarge the knowledge on damping characteristics of materials produced by additive manufacturing. The data from this characterization will be input on the prediction model, and as a result, design improvement is envisioned. In order to obtain this, the main tasks of this activity will include:
;
-
- Selection of study case of a vibration sensitive application.
- Development of simulation / prediction model from damping behaviour on AM materials.
- Characterization of the damping properties of bulk AM materials, as means to determine the baseline for this technology.
- Re-design test samples geometry, e.g. material, cavity dimensions, shape, taking into account the results from Tasks 2 and 3.
- Test the re-designed samples.
- Validate the prediction model and refine it based on the results obtained in Task5.
- Produce and test an engineering model from the study case selected in Task 1.
;
;
Application Domain
Generic Technologies
Technology Domain
15 - Mechanisms
20 - Structures
24 - Materials and Manufacturing Processes
Competence Domain
2-Structures, Mechanisms, Materials, Thermal
Keywords
38-Advanced Manufacturing
Initial TRL
TRL 3
Target TRL
TRL 4
Achieved TRL
TRL 5
Public Document