Sustainable Thermal joint workmanship validation by smart material
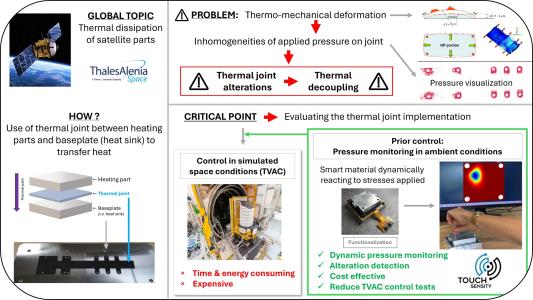
Thermal dissipation is a recurrent issue in systems and a real concern in satellite thermal joints for space companies such as Thales Aliena Space (TAS). This problem is addressed with time-consuming and costly tests under simulated space conditions (using TVAC). This study aimed to implement Touch Sensity (TS) solution to detect eventual thermal decoupling in thermal joints via pressure monitoring in order to enhance joint workmanship validation process. Functionalizing joints with TS sensing device enabled a pressure distribution visualization at the interface. This implementation provided repeatable and consistent results under ambient and space conditions.
The main goals of this project were:
- the integration of TS sensing device into a TAS typical configuration,
-
the validation of TS technology response through its abilities:
- to assess the strains the thermal joints endure,
- to withstand space environmental conditions.
In the early steps of the project, combinations of the TS sensing device with thermal joints (A,B,C) were investigated. The configurations were evaluated on the following criteria:
a) evaluation of the global applied pressure,
b) cartography of pressure distribution at the interface,
c) resistance to high pressure and temperature,
d) defect cartography.
After selecting the most promising sensing device in terms of pressure response, despite its intrusive implementation, its sensing properties have been approved in combination with the thermal joints A and C. The sensing device provided repeatable and consistent responses for the above-mentioned criteria a) to c). Regarding criteria d), the first results of the defect cartographies displayed areas altered by introduced defect (lack or excess of thermal joint), but they lacked precision.
Further investigations were successfully conducted to improve the defect cartography, implying some adjustments (the use of joint D and a specific Sensity Tech ® calibration). The adjustments enabled a significant improvement of the defect cartographies, as the sensing devices were able to detect and locate defects close to the target size. This dedicated process provided repeatable and consistent results.
Considering these results, it was decided to process the sensing device evaluation under space environmental conditions (vacuum and temperature) using joint D as the first step, to avoid misinterpretations related to thermal joint A, B or C. The defect cartographies for these joints need to be studied in further detail and will be addressed in future projects.
The tests under space environmental conditions (using TVAC machine) have shown that the TS technology withstood all the imposed pressure and temperature conditions, providing coherent cartographies of the defect.
Thus, from the beginning of this OSIP, the objectives and configurations were revised and simplified as the technical constraints were gradually discovered. Lessons have been learnt, and the technology was improved leading to its validation in those simplified configurations.