Consolidation of mN-FEEP Thruster Performance (mN-FEEP 4)
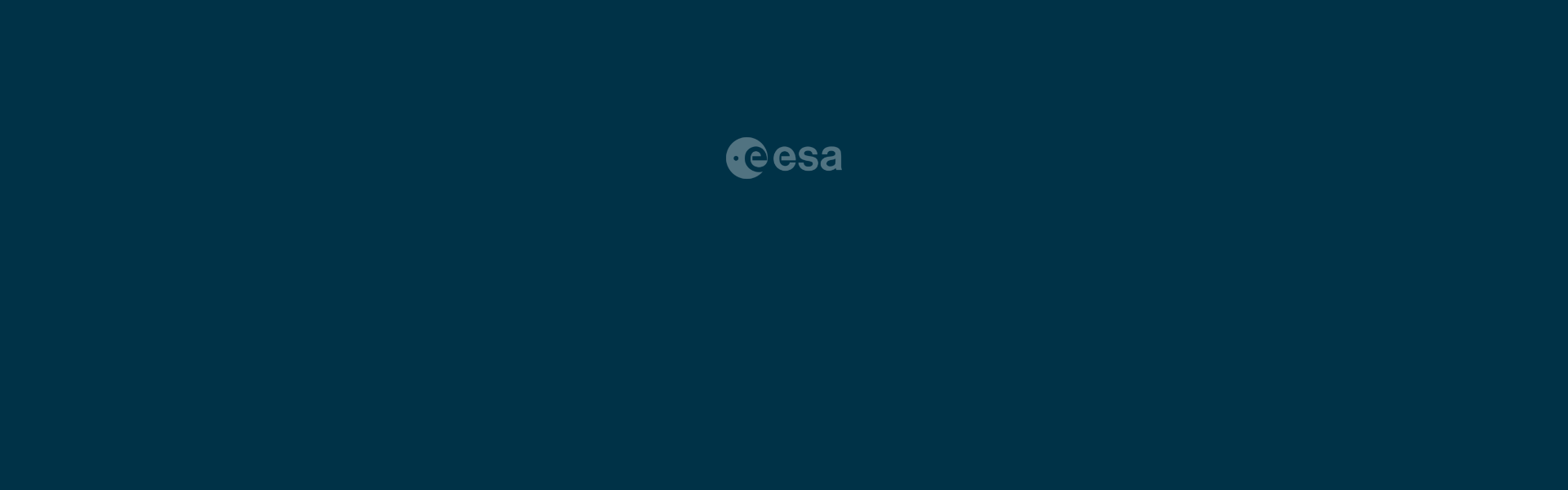
The proposed activity aims to achieve:- An improved understanding of pertinent emitter characteristics by increasing the number of manufactured and characterized units- optimization of the wetting process and the electrode configuration
The first steps have been taken to establish a non-explosive, harmless Indium-based 100W electric propulsion system for small and medium satellites. The activity successfully developed a breadboard that included all necessary functions for controlling a micro thruster, including temperature sensing and control, generation of the high voltage supplies for the ion emitter and extractor as well as heating and bias voltage supply for the charge balancing.
Next Generation Gravity Missions will require microthrusters to compensate the drag of several spacecraft flying in formation. Porous mNFEEP thrusters are important candidates for this task.The sharp, porous tungsten crown emitter used in the mN-FEEP thruster is capable of producing thrust from the ?N-range to the mN-range. Furthermore, the technology has undergone an additional level of refinement in that the porous matrix, which is crucial to the operation, has been varied in grain size and sintering techniques in order to find the most suitable candidate. The crown emitter is first manufactured and then wetted with indium in a distinct wetting facility. It is then installed in the thruster module and the initial start-up, the so called "priming"; is performed at high emitter currents. Once the emitter is fully operable, it can be operated continuously with lower currents. The behaviour of the emitter during priming and the resulting thruster performance highly depends on the quality of the wetting process. This is also reflected in the necessity of high start-up-voltages compared to the nominal operation voltages.Two main activities have been identified as the most valuable for this investigation. They focus on different potentials for improvement of the thruster performance or the manufacturing process and aim to establish a large data base correlating the manufacturing process with thruster performance.1.Characterization of the start-up behaviour and optimization of the wetting procedure: Implement the capability to monitor all individual emission sites of the crown emitter during the start-up phase. Manufacture a large sample of similar crown emitter, using the optimized manufacturing process found in previous activities. Investigate the start-up behaviour of a large number of crown emitters wetted with different wetting procedures and find a wetting procedure that maximizes firing homogeneity and/or minimizes the voltages required for the start-up phase. Investigate the repeatability of the chosen wetting procedure by applying it to a large number of crown emitters and testing the reliability of the predicted start-up behaviour.2.Assessment of the mass efficiency of the thruster:Measure the mass efficiency of a large number of crowns at various operating points, where all crows should be manufactured and wetted with the same previously optimized procedures. The sample size should allow for a statistical analysis of the mass efficiency over the complete thrust range of the thruster.3.Assessment of the thrust characteristics of the thruster: Measure the thrust characteristics of a large number of crowns at various operating points, where all crowns should be manufactured and wetted with the same previously optimized procedures. The sample size should allow for a statistical analysis of thrust and ISP over the complete performance map of the thruster. Analyze the results of this task together with the mass efficiency measurements conducted in Task 2 with respect to the performance of the used electrode configuration and investigate the potential for optimization of this configuration.