Metallic Glasses for High Performance Mechanism Applications on Long Term Missions
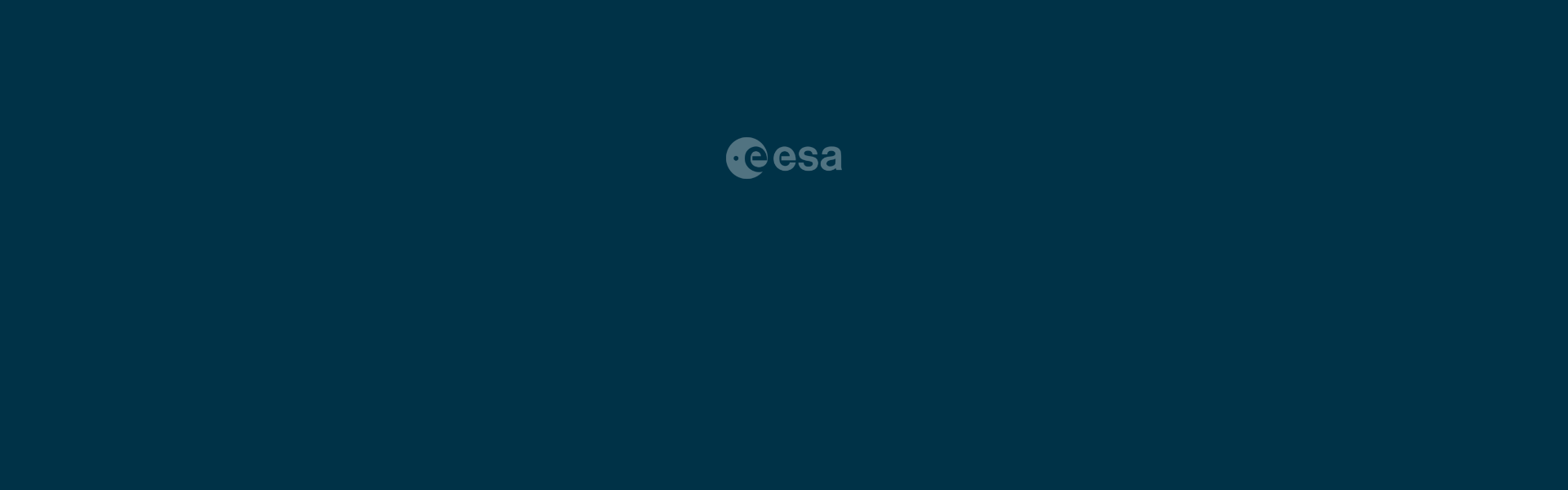
This activity is aimed at applying the attractive properties of metallic glasses (i.e. high strength, high hardness, high elastic strain, high energy storage and restoration ability) to enhance the performance of mechanism components (life, resistance to launch loads, mass reduction).
Metallic Glasses (MG) are a class of alloys which retain an amorphous structure in the solid state, when cooled from the liquid state. Formation of a fully amorphous structure for large cross sections (up to > 1 cm) is now possible for several alloying systems referred to as Bulk Metallic Glasses (e.g. Fe-base, Ti-base, Al-base, Mg-base, Ca-base, Zr-base). The lack of long-range order and the absence of microstructural features (grain boundaries, phase boundaries, segregation) confer attractive properties to MGs, such as high yield strength (up to several GPa), high specific strength, high hardness, high wear resistance, high resilience (ability to store and return elastic energy) and low mechanical damping (i.e. low energy loss). MGs are also characterised by a high elastic strain limit, low Young modulus and a very high magnetic permeability. From a processing point of view, the high viscosity of MG alloys in the supercooled liquid state (i.e. above the glass transition temperature) offers possibilities for thermoplastic forming to complicated shapes, with high dimensional accuracy and very good surface finish. A very good surface finish can also be obtained by moulding or polishing, due to the lack of grain structure. Metallic glasses can also be deposited as thin films with excellent surface finish. Additive Layer Manufacturing techniques have also recently been demonstrated to successfully produce MG material, which virtually removes limitations in part geometry and part thickness. The combination of properties offered by MGs is highly interesting for mechanism applications where high wear resistance, high hardness, good surface finish (bearings balls and races, gears), as well as high elastic strain and energy restoration ability (springs, membranes) are of importance. Low magnetic signature is also required for mechanism components, which can be offered by MG materials. Fe-base MGs or other compositions appear promising to replace currently used stainless steels and enhance the performance of mechanism components. Harnessing the properties of MGs could lead to components with longer lives, higher resistance to launch loads and reduced dimensions, to support longer and more demanding missions. In this activity, alloy compositions and suitable production processes for applications in mechanism parts (gears, bearings balls and races, springs, membranes) will be investigated and down-selected. Samples of metallic glass material will be produced and characterised against the requirements for the intended applications. The activity consists of the following tasks: - A review of suitable MG alloy compositions will be performed, to fulfil the requirements associated with mechanism components for space applications (e.g. gears, bearings balls and races, springs, membranes). - Suitable processes for the production of MG mechanism parts will be reviewed and identified. Processes allowing the production of bulk metallic glass parts (e.g. Additive Layer Manufacturing, casting, thermoplastic forming) will be considered. Alternatively, processes allowing the application of MG material coatings on bearings and gears elements to reduce friction and cold welding will also be addressed. - Specimens of the selected alloy compositions will be produced by applying the selected processes. - The specimen properties will by characterised against the requirements of the intended mechanism applications: mechanical properties (e.g. HCF, creep, hardness, strength), corrosion, SCC, friction, CTE, coating compatibility, lubricant compatibility, magnetic field emission.