Real-time verification and testing facilities for image processing for navigation
Programme
GSTP
Programme Reference
G617-282SA
Prime Contractor
ASTOS SOLUTIONS GMBH
Start Date
End Date
Status
Closed
Country
Germany
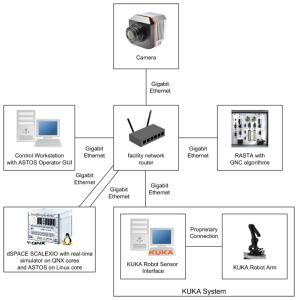
Objectives
The objective of this activity is the design and development of a reconfigurable and high fidelity testing facilities for GNC verification.
Description
The facilities shall be suited for any space flight mission specially those relying on image processing for navigation (visible, infrared, multispectral, LIDAR). The facilities shall support MIL, SIL, PIL, and HIL verification types, and shall allow testing in open-loop and closed-loop configurations. Subsystem aspects shall be considered to cover interdisciplinary verification aspects. The facilities shall be modular, supporting fast and flexible scenario configuration and shall be movable and relocatable. The goal is to achieve faster, less expensive, more flexible, and more modern GNC verification and validation.
;
This activity shall provide such a facility by adapting and enhancing of the current COTS elements within the following tasks:
;
- Design and prototyping of the test facilities - The overall design of the test facility shall be defined covering all aspects of MIL, SIL, PIL and HIL including navigation with image processing sensors. A fluent workflow shall be provided. A subset of hardware interfaces shall be selected to demonstrate the HIL functionality including protocols and interface software. The facility shall receive a graphical MMI that allows for test execution and monitoring scenario configuration and error injection. The MMI shall comprise plotting and animation capabilities for recorded simulations and real-time data.
;
- Task 2: Extension of the simulator - The simulator shall be extended to fulfill all requirements of the test facility. Especially performance aspects shall be considered, which allow running also multi-body and flexible body simulations for e.g. space robotic scenarios. Critical real-time aspects shall be identified and assigned to application cases based on the required time steps.
;
- Task 3: Extension of the Camera Simulator - The Camera Simulator shall be extended to provide the image data in the applicable spectrum. Further, extension is needed to cover arbitrary Lidar scan patterns and flash Lidars. Then, an interface between Camera Simulator and software shall be implemented: the Camera Simulator shall receive from local temperatures needed for image generation in the thermal infrared regime; shall receive irradiance and shadowing information that shall be used to improve the modelling of sun sensors and solar cells, as well as the thermal model itself.
;
- Task 4: Demonstration and evaluation - The functionality shall be demonstrated for the complete workflow. A counterpart in terms of a LEON board with a subset of supported interfaces shall be used for the demonstration.
;
The facilities shall be designed for industrial maintainability and long-time availability. It shall be based on commercial-off-the-shelf items, namely dSPACE processing units and interface cards, a real-time generator for raw image and Lidar data, and a dynamics, environment and equipment simulator that supports complex GNC design and subsystem analysis tasks. The use of dSPACE products for GNC prototyping in European space industry and ESA occurs along two classes of test benches: Processor In the Loop (PIL) and Hardware In the Loop (HIL). AOCS and GNC rapid and lightweight prototyping is achieved by using PIL and HIL environments. The dSPACE products are heavily used for SCOE applications in the automotive and aeronautical industry. The modular design that is split into processing units and interface cards is ideal for a universal facility that is not designed for a specific spacecraft but must be reconfigurable for various applications. The corresponding tool chain allows for adaptations of interface algorithms like protocol implementations, whereas such changes can be made even by a user.
;
Changes are covering budget, scope and the duration of this activity.
During the implementation of the activity quot;Real-time verification and testing facilitiesquot; (RTFIP), the need for further improvements, extension of use cases and validation of the test bench arose in order to satisfy customer needs in the shortest possible time.
The developed testbench offers a solution which is completely based on COTS components and covers the workflow over the whole lifecycle starting with Phase 0 and ending with EGSE/SCOE. In order to be ready for operational use an extensive validation campaign with final improvements are required.
The following tasks are added to the original description of the activity:
-
- Technical Improvement. Including:
- Improvement of the CPU performance. This is required for utilization with real-time applications which required update rates higher than 40 Hz, i.e. an integration frequency of at least 160 Hz. An improvement of 50% is expected for closed loop simulations.
- Modifications, which are required to run the new test case: VEGA-like 4 stages end to end launcher scenario, from lift off to payload insertion:
- Improvement of modules. This concerns mainly algorithms related to the handling of massive output data during the simulation output.
- Integration of the RTFIP development into the commercial trunk, which makes the technology available to all application cases.
;
-
- The validation task focuses on the utilization of the software in a test case different from the ones used in the past. A test case from the LGSST (Launcher GNC Simulation and Sizing) project shall be used to keep the effort for the new test case small. The existing results of the MIL simulations shall be compared against PIL simulations using the RTFIP technology. The LGSST test case supports in addition to the original RTFIP:
- Flexible body dynamics defined by sloshing propellant and a flexible slender body
- Perturbations due to wind
Phasing and separation of stages, which require additional management software and mode management
;
Application Domain
Generic Technologies
Technology Domain
5 - Space System Control
Competence Domain
3-Avionic Systems
Initial TRL
TRL 5
Target TRL
TRL 6
Public Document
Executive Summary
Executive Summary
Final Presentation
Executive Summary