De-risk assessment: 22N Thruster Maturation
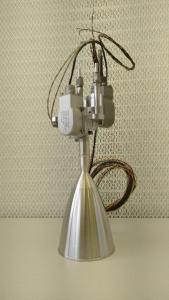
The program was intended to derisk the development of the S25 thruster via the structural upgrade of a first STM model (EM1), and a hot fire demonstration to collect preliminary performance data. This phase was also intended to validate few design concepts with i.a. the introduction of a cartridge-like coaxial injector mounting (less components with a radial instead of an axial component sealing, compared to the S10 heritage injector), a welded nozzle expansion made of a NiCr-alloy, replacement of the heritage Nimonic-75 by Alloy-718 and -690 for the injector housing and the chamber heat barrier.
Achievements and status: During a hot fire campaign (TRL-6), the thruster engineering models (EM1 and SN2) have proven ability to perform within the nominal operational pressure box of a standard GEO CPS specification. The thruster demonstrated low thrust roughness and margin against combustion instabilities for a wide throughput range. The maximum recorded throat temperature, slightly above 1300°C, shows margin against the platinum-alloy limits. In pulse mode, the thruster shows very efficient and repeatable behavior with stable thermal signature (no thermal runaway observed in the tested area) for a large domain from single low impulses (MIB) below 100 mNs to quasi steady state firing (off-modulation). During pure steady state firing the engine was tested between 16N and 30N thrust.
Benefits: With an efficient behavior from repeatable very low impulses up to high delta-v capabilities, the S25 thruster demonstrated to be an European option to fill a gap between the heritage 10N and 200N thrusters, especially for interplanetary missions or lander applications.