Embedded thermal control of an active antenna using 3D printing
Programme
GSTP
Programme Reference
GT17-137TIc
Prime Contractor
THALES ALENIA SPACE FRANCE
Start Date
End Date
Status
Closed
Country
France
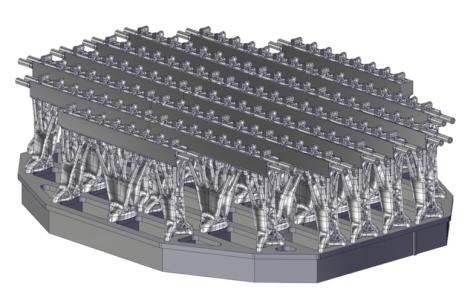
Objectives
Objective(s):
•Development of an advanced active antenna structure, made by additive manufacturing, with embedded thermal control connected to the satellite two phase Mechanical Pumped Loop, that can manage huge power budget.
•Validation of a methodology for both the design and models construction that can be applied to any type of active antenna.
Description
Background and justification :
•The use of active antennas with very high dissipated power has been increasing (up to 7kW). However, the current thermal management is efficient for quite low dissipated power and a new thermal control is needed for future antennas with very high value of dissipated power. A previous ESA study showed that a Mechanically Pumped Loop (MPL) is very well suited for the thermal control of active antennas.
•Moreover, the use of additive manufacturing (AM) technologies has a high added value for performance increase and innovation. Combining these developments in AM with the advances in MPL systems will allow the realization of an embedded thermal control solution for antennas with very high dissipation power.
•Finally, since 2019, a study on the Space Inspire satellite has been conducting on the development of an active antenna with MPL but through conventional processes of manufacturing.
Achievements and status:
•The feasibility of an active antenna with embedded thermal control using additive manufacturing is demonstrated by fulfilling all the requirements and the smooth running of manufacturing.
•The reliability of simulations is proved thanks to a good correlation between predictions and tests results.
•In case of further development, points remain open : long-term ammonia compatibility with AM alloy (beyond project scope), bi-metallic welding, cleanliness and particle release.
Benefits:
•The developed solution is a smart, robust and flexible solution for future high capacity transmit phased array antennas using the satellite two phase MPL where there is a strong drive towards lowering the cost of satellite capacity in orbit, leading to the emergence of the flexibility and high throughput systems featuring large numbers of beams.
•The thermal acceptance test of the antenna assembly could be done at antenna module level instead of satellite level in case of conventional manufacturing that leads to a simplification and securing of the AIT sequence.
Application Domain
GEN-Generic Technologies
Technology Domain
21 - Thermal
Competence Domain
2-Structures, Mechanisms, Materials, Thermal
Keywords
99-Others
Initial TRL
TRL N/A
Target TRL
TRL N/A
Achieved TRL
TRL 5
Public Document
Final Presentation
Executive Summary